Ein Blick ins Hochofenwerk – hinter den Kulissen bei ArcelorMittal in Bremen
ErfolgsgeschichtenEine Werksbesichtigung des Stahlwerks Bremen
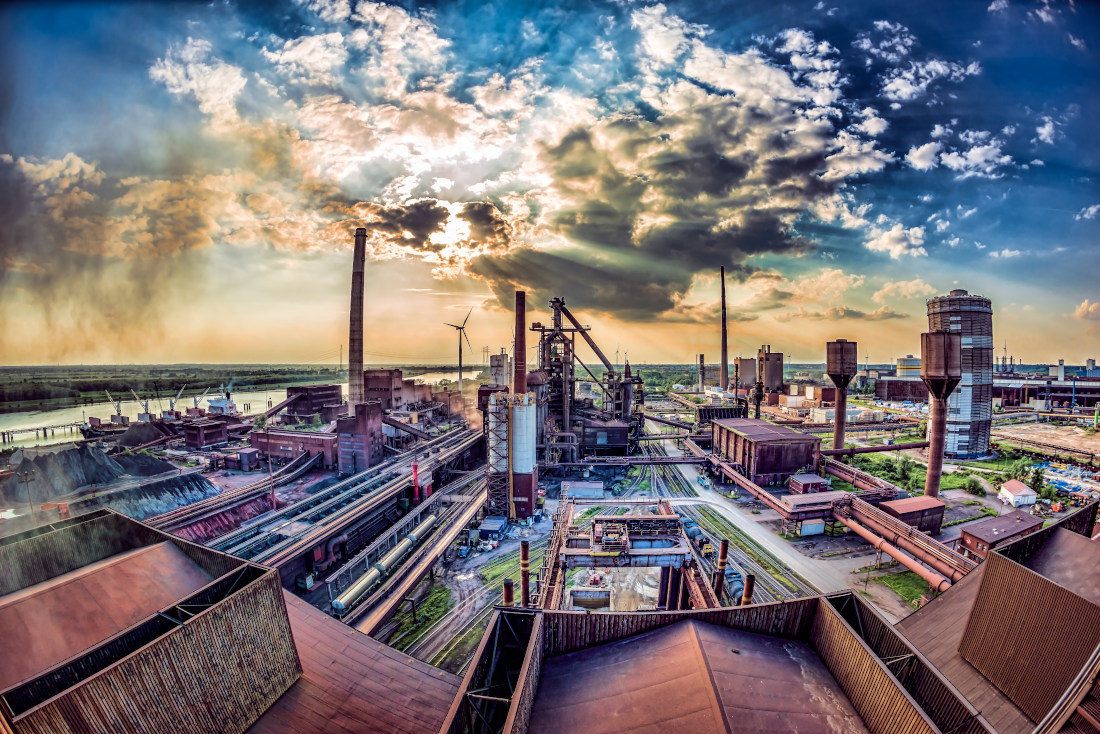
Eine Besichtigung des Stahlwerks in Bremen lohnt sich: Der Anblick der Hochöfen oder von hunderten Tonnen flüssigen Eisens lassen nicht nur Kinderaugen groß werden. Wir haben eine Tour durch das Werk von ArcelorMittal Bremen gemacht – und sind dabei auf Überraschendes gestoßen.
Nach dem Anlegen von Sicherheitskleidung – Jacke, Brille, Handschuhe, Helm – fahren wir mit dem Bus über das Gelände. Die erste Überraschung: wie grün es ist. Das Gelände des Stahlwerks misst sieben Quadratkilometer, ist größer als die Bremer Innenstadt. Viele Teile des Geländes sind begrünt, zwischen den einzelnen Werksbereichen ist viel Platz, wir entdecken sogar einen kleinen Weiher.
Der Hafen: Umschlagplatz
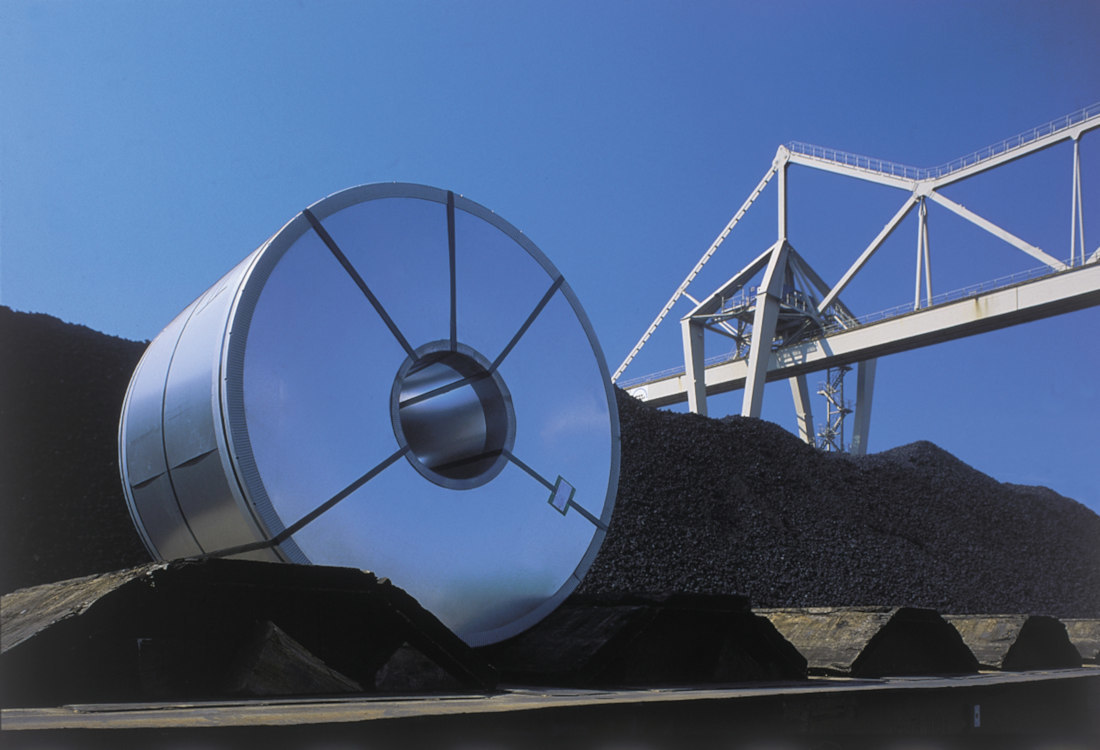
Und doch werden hier rund 3,6 Millionen Tonnen Stahl im Jahr produziert. Einen ersten Eindruck davon erhalten wir am Hafen, wo unter anderem die Rohstoffe für die Stahlproduktion angeliefert werden. Und hier stehen auch schon die ersten Coils, Rollen aus gewalztem Stahl, das Endprodukt des Stahlwerks, bis zu 45 Tonnen schwer. Sie werden von hier mit dem Schiff abtransportiert. Insgesamt acht Millionen Tonnen schlägt der Hafen jährlich um.
Der Hochofen – Höllenfeuer inklusive
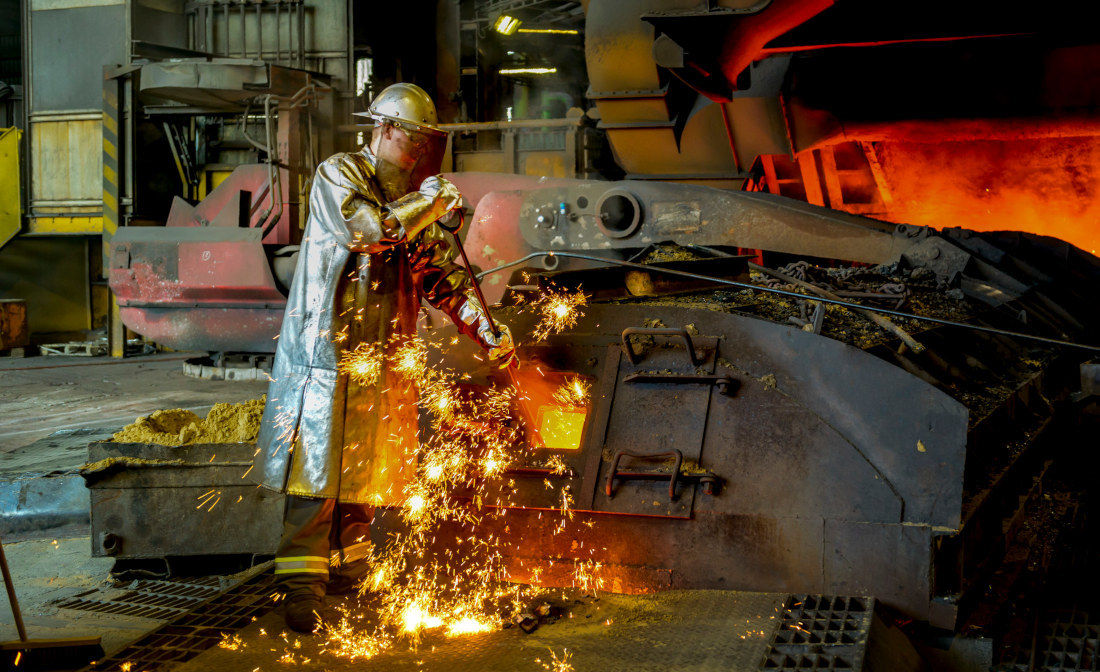
ArcelorMittal Bremen ist ein sogenanntes vollintegriertes Hüttenwerk: Alle Anlagen von der Roheisenerzeugung bis zur Feinblechverarbeitung sind auf dem Gelände vereint. Die Rohstoffe gelangen über Förderbänder in die Hochöfen. Dort wird das Eisenerz zu Roheisen reduziert.
Die Besichtigungstour führt uns direkt in den Bereich des Hochofenwerkes zum Abstichloch – des rund 110 Meter hohen Hochofens 2. Ein beeindruckender Anblick, wenn das flüssige Roheisen aus dem Abstichloch fließt. Das rote Glühen erinnert an flüssige Lavaströme oder Szenen aus dem Reich Mordor aus der „Herr der Ringe“.
Im Stahlwerk – aus Eisen mach Stahl
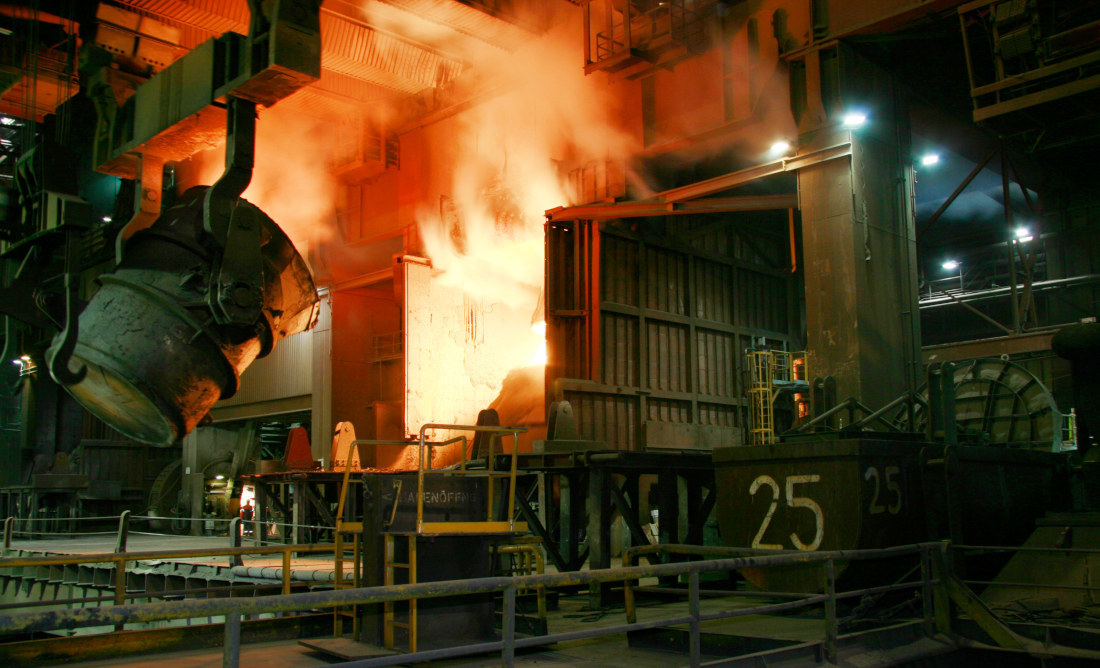
Auch das flüssige Roheisen ist nur ein Vorprodukt. Um Stahl zu erzeugen, muss ihm noch Kohlenstoff entzogen werden. Das geschieht bei der nächsten Station, im Stahlwerk. Ein Eisenbahnwaggon – der sogenannte Torpedowagen – transportiert das knapp 1.400 Grad heiße Roheisen vom Hochofen ins Stahlwerk. Hier wird es in einen gigantischen Behälter umgefüllt, die sogenannte Roheisenpfanne: Ein feuerfestes Gefäß mit 350 Tonnen Fassungsvermögen, welches an einem Kran durch eine Halle gefahren wird.
Sein Ziel ist ein weiterer Behälter, der Konverter, in dem mittels einer Lanze Sauerstoff in das flüssige Eisen geblasen wird. Der Sauerstoff reagiert mit dem Kohlenstoff im Eisen zu CO2. Neben dem Sauerstoff werden hier noch weitere Stoffe dem Eisen hinzugefügt. Noch im Stahlwerk kühlt die Masse ab und wird zu den sogenannten Brammen gegossen – langen Stahlblöcken.
Wo rohe Kräfte sinnvoll walten – im Warmwalzwerk
Die Besichtigung des Stahlwerks Bremen führt uns nun in das Warmwalzwerk. In der einen Kilometer langen Halle wird aus den Brammen ein Warmbreitband gewalzt. Die Eisenblöcke werden zunächst auf 1250 Grad erhitzt und gelangen dann rotglühend auf die Walzstraße. Selbst vom Besuchergang, 10 Meter von der Walzstraße entfernt, ist die Hitze der Bramme deutlich zu spüren.
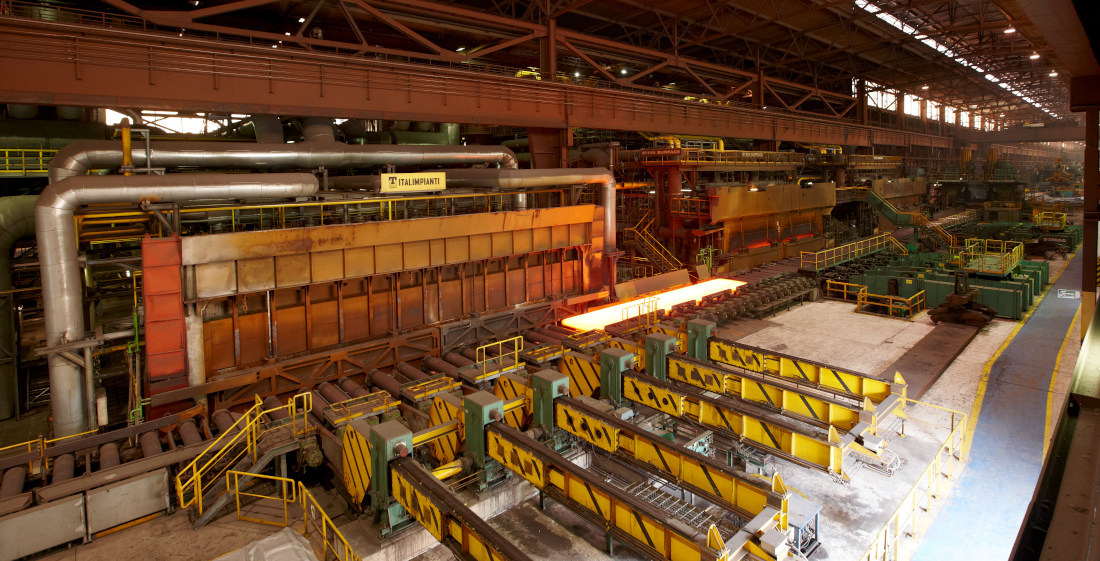
In dem Produktionsprozess wird das Stahlprodukt allmählich dünner gewalzt – wie bei einer Nudelmaschine, nur in viel größer. Und wie der Nudelteig wird auch das Stahlband immer länger, aus der Bramme wird am Ende ein mehrere hundert Meter langes Stahlband, das zu einer Rolle, dem sogenannten Coil, gewickelt wird. Während des Walzens verdampft das Kühlwasser in großen Wolken.
Finalisierung in weiteren Werksbereichen
Unsere Besichtigung des Stahlwerks endet hier – denn nicht alle Werksbereiche konnten aus Zeitgründen besichtigt werden. Die Reise des Stahls geht jedoch weiter: Während einige Coils direkt an den Kunden versandt werden, werden andere Coils weiterverarbeitet. Was bleibt sind vielfältige Eindrücke – von den gigantischen Maschinen und Anlagen, dem komplexen, aber wohlgetimten Ablauf. Von der hochautomatisierten Arbeit, welche von den 3.600 Mitarbeiterinnen und Mitarbeitern im Drei-Schicht-Betrieb überwacht, überprüft, unterstützt und durchgeführt wird. Und natürlich vom Stahl, der vielfältig weiterverarbeitet wird. Wie zum Beispiel in der Automobil-, Bau- oder Haushaltsgeräteindustrie.
Wer nun selbst einmal das Stahlwerk besichtigen möchte: bremen.arcelormittal.com/Vom-Erz-zum-Stahl/Werksbesichtigungen/
Erfolgsgeschichten
Dicht an den großen Schiffen vorbei
Nach langer Pause können Gäste wieder zu Rundfahrten durch den Bremerhavener Fischereihafen starten. Damit lässt Maice Hissenkämper eine Tradition aufleben, die ihr Vater vor 30 Jahren begründet hat. „Die Tour ist ganz anderes ist als herkömmliche Hafenrundfahrten“, verspricht Mark Lippert, Matrose auf der „Lady Sunshine“. Sie ist eine Zeitreise zu vielen selbst Einheimischen unbekannten Details.
zur BIS BremerhavenWas ist ein Sozialunternehmen?
Die Zahl der Sozialunternehmen nimmt seit Jahren zu. Aber was heißt „Sozialunternehmen“ eigentlich genau? Und was unterscheidet sie von anderen Wirtschaftsformen? Eine Erklärung.
Mehr erfahrenEssbare Gärten
Volker Kranz gehörte mit zu den ersten, die in den 1990er-Jahren die Idee der Permakultur nach Deutschland brachten. Seitdem ist die Nachfrage nach nachhaltigen Gärten stark gestiegen. Die von ihm in Bremen gegründete Landschaftsbaufirma baumrausch plant und erstellt europaweit ökologisch wertvolle Grünflächen – so wie auch den Waldgarten der Autorin Cornelia Funke.
Mehr erfahren