Flugzeugbau hautnah – hinter den Kulissen von Airbus in Bremen
Luft- und RaumfahrtLuftfahrt "Made in Bremen"
4.500 Beschäftigte arbeiten am Airbus-Standort Bremen auf 450.000 Quadratmetern oder 63 Fußballfeldern. Straßenzüge, Fahrradwege, unzählige Gebäude und Hallen, das Areal erscheint riesig und ist mit bloßem Auge kaum zu überblicken.
So unaufgeregt das Treiben auf dem Gelände aus der Vogelperspektive wirkt, so beeindruckender ist das, was in den zahlreichen Hallen und Gebäuden geschieht: Industrieleistungen auf Spitzenniveau.
Dank Bremen geht es hoch hinaus – und sicher wieder runter
Bremen ist der zweitgrößte Airbus-Standort in Deutschland, beheimatet in der Airport-Stadt auf dem Gelände der früheren Focke-Wulf-Flugzeugbau AG (später Vereinigte Flugtechnische Werke), die bereits 1924 ihren Betrieb aufnahmen.
Als erste Station auf einer Rundtour durch das Werk erwartet uns die Landeklappen-Fertigung. Die Landeklappen befinden sich an den Tragflächen eines Flugzeuges. Sie sorgen für mehr Auftrieb bei niedrigen Geschwindigkeiten, also bei Start und Landung.
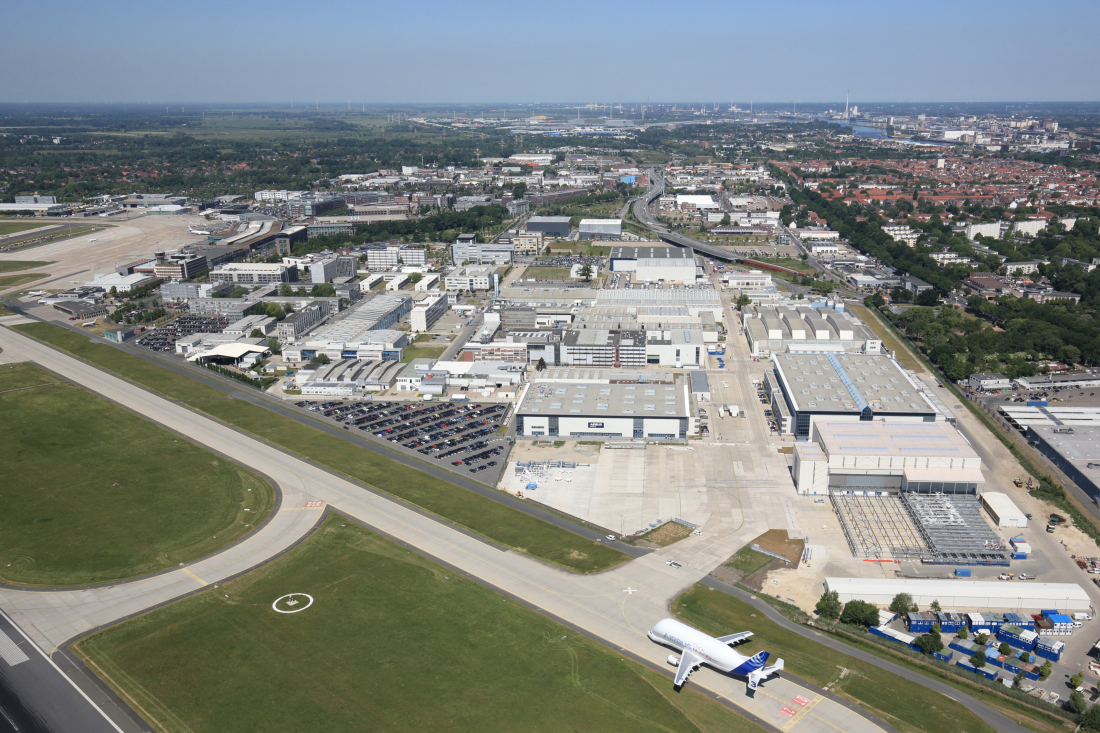
Hier reiht sich eine Landeklappe an die nächste. In Bremen werden sie für alle Airbus-Flugzeugmodelle gefertigt. Valeska Tramp, aus der Kommunikationsabteilung von Airbus in Bremen und eine unserer Begleiterinnen an diesem Tag, erklärt, wie die Produktion abläuft: „Jedes Teil hat hier seinen Platz. Die Produktion erfolgt systematisiert und just-in-time. Einige Arbeitsschritte sind noch echte Handarbeit.“
Im Jahr werden in Bremen rund 2.300 Landeklappen verschiedener Typen produziert. Während die innere Klappe der A320, des kleinsten Flugzeugtyps von Airbus, „nur“ 4,4 Meter lang und 1,2 Meter breit ist, messen wir bei der A330 über zehn Meter. Ein Größenunterschied, der schon mit bloßem Auge gewaltig erscheint. Jeder Flügel verfügt über zwei Landeklappen, die von Lackierrobotern vollautomatisiert angestrichen werden.
Von den Landeklappen zu den Flügeln im Airbus-Werk Bremen
Noch „gewaltiger“ geht es in der nächsten Halle, der Flügelausrüstung, zu. An vier Stationen werden in Bremen Großbauteile, Hydraulikleitungen und mehrere Kilometer an Elektrikleitungen in die Tragflächen der Langstreckenflugzeuge A330 und A350 eingebaut. Kommen die A330-Flügel noch im leeren Zustand mit einem Gewicht von circa 13 Tonnen aus England in Bremen an, verlassen sie acht Tage später die Hansestadt Richtung Toulouse ausgerüstet mit bis zu sieben Tonnen mehr. Diese voll ausgerüsteten Flügel werden dann per Airbus-eigenem Frachtflugzeug, der „Beluga“, zur Endmontage geflogen. 150 Flügelpaare entstehen auf diese Weise pro Jahr.
Ab 2025 wird sich Bremen verstärkt auf die Hochauftriebssysteme konzentrieren, wozu die Landeklappen gehören: Dann wird ein Großteil der Produktion der inneren Landeklappen für die A321 in Bremen stattfinden, während die A330-Flügelausrüstung in Großbritannien stattfinden wird.
In Bremen werden die Klappen und Flügel aber nicht nur produziert bzw. ausgerüstet – Airbus betreibt hier sein Entwicklungszentrum für die Hochauftriebssysteme. Ingenieurinnen und Ingenieure forschen daran, Klappen und die damit verbundenen Antriebe für die nächste Generation an Airbus-Flugzeugen zu entwickeln und für die derzeitigen Modelle zu verbessern.
Eine Halle weiter zeigt sich, warum der Standort auch das Kompetenzzentrum für die Technologieentwicklung, Industrialisierung und Produktion von komplexen metallischen und thermoplastischen CFK-Bauteilen im Airbus-Konzern ist. Hier werden in drei Produktionslinien hochintegrale Umformteile aus CFK und Metall für nachhaltige Produktionsprozesse gefertigt. Derzeit wird eine der weltweit größten CFK-Pressen aufgebaut, mit der zukünftig die größten thermoplastischen CFK-Bauteile der Welt in Bremen produziert werden. Zudem werden von diesem Standort Kunden in aller Welt binnen 48 Stunden mit digital getrackten Ersatzteilen versorgt.
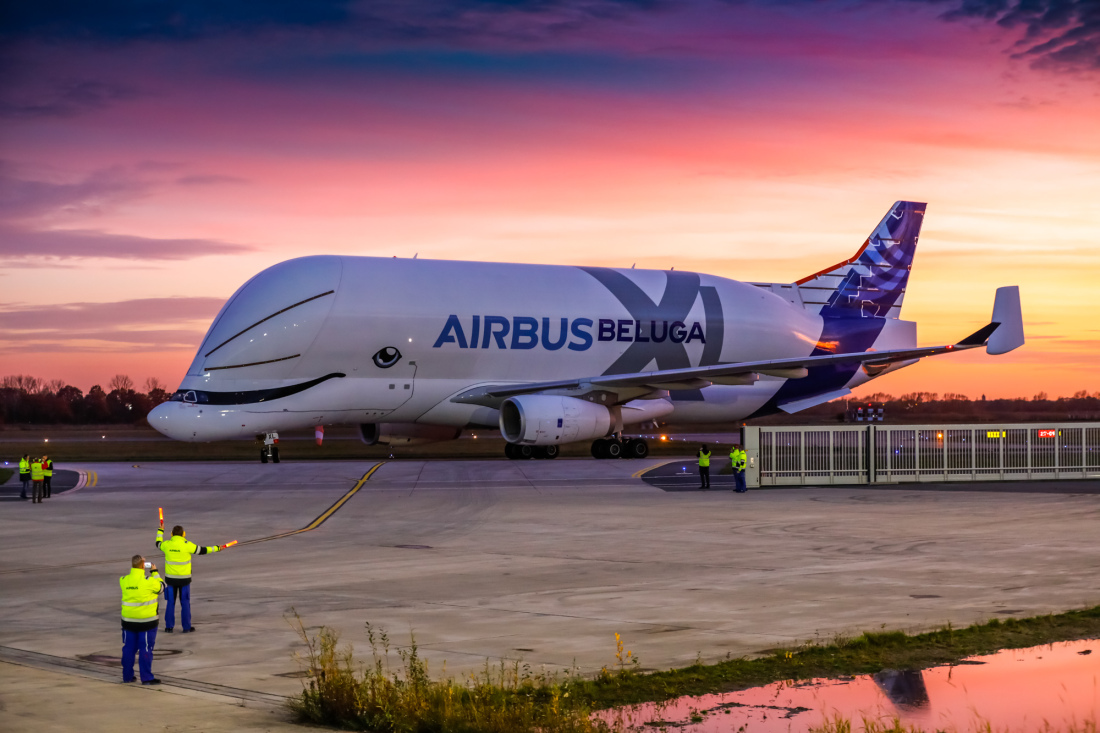
Groß, größer - A400M
Weiter geht es zur A400M, dem modernsten Militärtransportflugzeug von Airbus, und damit in die dritte Halle. In Bremen ist die Entwicklung und Montage des Rumpfes der A400M angesiedelt. Und sogleich empfängt uns auch der riesig erscheinende Rumpf einer A400M. Wir fragen nach, ob sich die Produktionsstandorte der A400M nicht untereinander Konkurrenz machen. Tramp verneint die Frage ohne zu zögern: „ Alle Airbus-Standorte ergänzen einander und bilden aufgrund ihrer verschiedenen Kompetenzen und Schwerpunkte ein funktionierendes und aufeinander abgestimmtes Netzwerk.“
In der Hansestadt wird der Großteil des Rumpfes montiert und mit Systemen ausgerüstet, bevor er per Beluga-Flug ins spanische Sevilla reist, wo die Endmontage stattfindet. Vorher bauen die Mechanikerinnen und Mechaniker aber noch das Frachtladesystem ein, das eine schnelle Be- und Entladung ermöglicht. Auch dieses System wurde in Bremen entwickelt.
Bisher wurden 178 A400M-Flugzeuge bestellt, 116 Stück ausgeliefert. Während die Produktion also noch einige Jahre weiterläuft, landete einer der ersten A400M-Prototypen mit dem Spitznamen „Grizzly 4“ im November 2022 nach zwölf Jahren unermüdlicher Test- und Erprobungsflüge in Bremen, um hier in den Ruhezustand zu gehen – Auf dem Airbus-Gelände wird das Transportflugzeug künftig als Ausstellungstück und Eventraum genutzt.
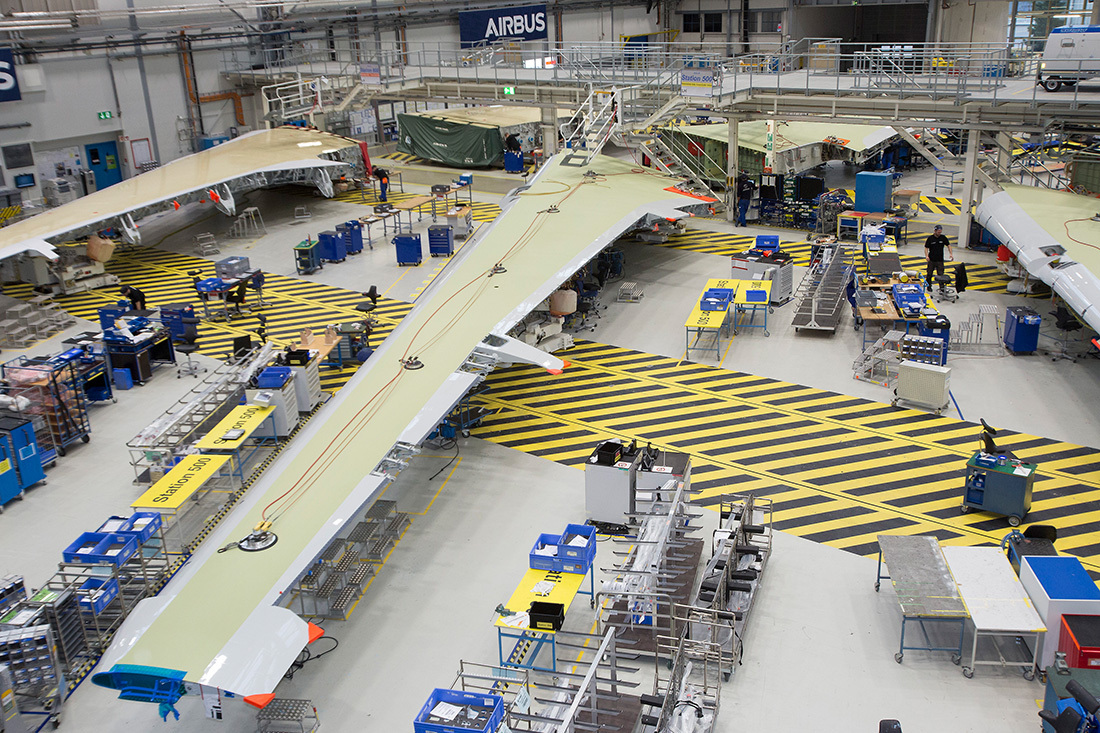
Die Zukunft der Luftfahrt mitgestalten
Rund drei Prozent aller CO2-Emissionen gehen auf das Konto der Luftfahrt. Das soll sich in Zukunft ändern; das klimaneutrale Fliegen steht in den Startlöchern. Airbus möchte etwa bis 2035 die ersten kommerziellen Flugzeugtypen auf den Markt bringen, die auf klimaneutralen Wasserstoff setzen. Zudem werden in Bremen die Belugaflugzeuge mit SAF – Sustainable Aviation Fuel betankt.
Was sich wie eine lange Zeit anhört, ist in Realität ein enger Zeitplan. Denn der neue Wasserstoff-Treibstoff benötigt ein völlig neues Flugzeugdesign, neuartige Technologien und Materialien, die erforscht, getestet und offiziell zugelassen werden müssen.
Dabei spielt der Bremer Standort eine wichtige Rolle. Denn hier versammelt sich viel Wissen um Tanksysteme, eine kritische Komponente für Wasserstoffflugzeuge. Zum einen hat Airbus hier eines seiner Zero Emission Development Center (ZEDC) eingerichtet. Zum anderen ist der Luftfahrtkonzern ein zentraler Partner im nahegelegenen Forschungs- und Entwicklungszentrum ECOMAT.
Das ECOMAT, gebaut und betrieben von der WFB Wirtschaftsförderung Bremen GmbH, vereinigt rund 500 Wissenschaftlerinnen und Wissenschaftler aus Industrie und Forschung im Bereich der klimafreundlichen Luftfahrt, Materialforschung, 3D-Druck und digitaler Flugzeugentwicklung. Wasserstoff-Tanksysteme und die neuen Materialien, die es dafür braucht, sind ein zentraler Gegenstand diverser Forschungsprojekte – genauso wie die gesamte Infrastruktur rund um den neuen Treibstoff.
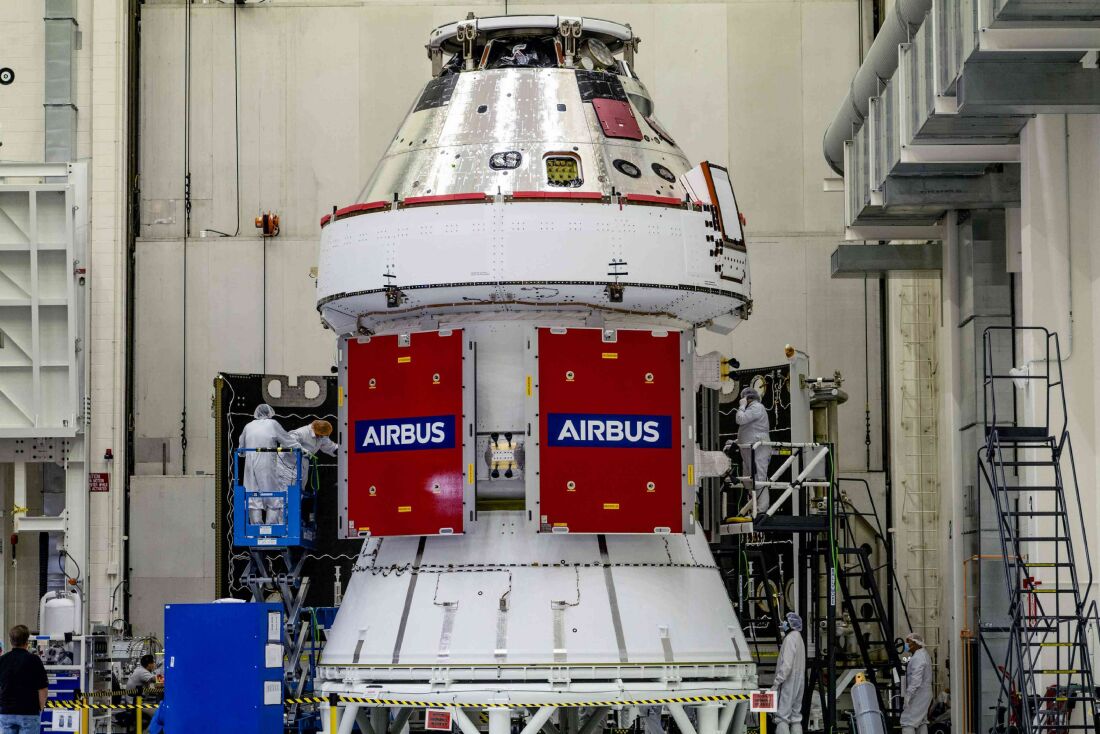
Raumfahrt aus Bremen
Der Grund für das große Tank-Know-how liegt im wahrsten Sinne des Wortes nahe – denn in der Bremer Airport-Stadt befindet sich auf dem Airbus-Gelände für kommerzielle und militärische Flugzeuge auch das europäische Kompetenzzentrum von Airbus für astronautische Raumfahrt, Weltraumrobotik und Oberstufen für Trägerraketen. Letztere werden mit in Tanks gespeichertem Wasserstoff angetrieben, die in Bremen produziert und entwickelt werden. Und so gelangt Wissen von der Raumfahrt in die Luftfahrt, auf kurzem Dienstweg sozusagen.
Rund 1.000 der 4.100 Airbus-Angestellten in Bremen arbeiten im Bereich Defence and Space. Hinzu kommen die Beschäftigten des hiesigen Standorts der ArianeGroup, einem Gemeinschaftsunternehmen unter Beteiligung von Airbus. Jede Ariane-Rakete startet mit einer Oberstufe aus Bremen ins All und auch die neue Mondmission der NASA – Artemis – absolvierte ihren Erstflug im Dezember 2022 mit einem Servicemodul aus Bremer Hand. Zudem stammt von hier das Weltraumlabor Columbus der Internationalen Raumstation ISS und alle europäischen Teile der Station aus der Hansestadt werden von hier verwaltet.
Und auch für die neue Ariane 6, die Ende 2023 zum ersten Mal starten soll, stammen die Oberstufen wieder aus der Stadt an der Weser.
Reparieren und Testen
Zum Airbus-Standort gehört in Bremen auch das Tochterunternehmen Testia, das sich auf Werkstoffprüfungen und die Ausbildung von Prüferinnen und Prüfern spezialisiert hat. Denn: Sicherheit geht vor. Das Unternehmen ist Partner am ECOMAT und beteiligt sich an Forschungsprojekten, etwa um Prüfungen mittels künstlicher Intelligenz zu ermöglichen.
Und last but not least: Fernab vom Werksgelände, im Industriegebiet Stuhrbaum vor den Toren Bremens, liegt das europäische Reparaturzentrum des Konzerns. Hierhin gelangen keine reparaturbedürftigen Flugzeuge – aber einzelne Komponenten, wie etwa Landeklappen, die hier instandgesetzt werden.
Es zeigt sich: Airbus ist der Dreh- und Angelpunkt der europäischen Luft- und Raumfahrtindustrie und Bremen hat daran als einer der großen Standorte eine zentrale Rolle. Dank interdisziplinärer Forschungsarbeit wird hier der Grundstein für viele weitere Jahrzehnte an Luft- und Raumfahrzeugen gelegt.
Interessante Stories aus Bremen auch in unserem monatlichen Newsletter:
Erfolgsgeschichten
Was ist ein Sozialunternehmen?
Die Zahl der Sozialunternehmen nimmt seit Jahren zu. Aber was heißt „Sozialunternehmen“ eigentlich genau? Und was unterscheidet sie von anderen Wirtschaftsformen? Eine Erklärung.
Mehr erfahrenEssbare Gärten
Volker Kranz gehörte mit zu den ersten, die in den 1990er-Jahren die Idee der Permakultur nach Deutschland brachten. Seitdem ist die Nachfrage nach nachhaltigen Gärten stark gestiegen. Die von ihm in Bremen gegründete Landschaftsbaufirma baumrausch plant und erstellt europaweit ökologisch wertvolle Grünflächen – so wie auch den Waldgarten der Autorin Cornelia Funke.
Mehr erfahrenMittelständische Unternehmen in Bremen, welche die ganze Bandbreite der Bremer Wirtschaft zeigen
Mittelständische Unternehmen bilden das Rückgrat der Bremer Wirtschaft. Sie schaffen Arbeitsplätze und produzieren weltweit nachgefragte Waren. Eine Auswahl von zehn Unternehmen, welche die Bandbreite der Bremer Wirtschaft zeigen
Mehr erfahren