Getting Up Close to Aircraft Construction – Behind the Scenes at Airbus in Bremen
AerospaceAviation "made in Bremen"
The Airbus facility in Bremen extends over 450,000 square metres, or 63 football fields, and has a workforce of 4,100. With its streets, cycle paths, myriad of buildings and halls, the premises are truly enormous and impossible to miss, even with the naked eye.
From a bird's eye view, activity at the site appears calm and unhurried, which makes what is actually taking place in the many halls and buildings even more impressive: Industrial performance at the highest level.
Thanks to Bremen, what goes up comes down again safely
Bremen is home to the second-largest Airbus plant in Germany. It is located in Airport City, on the site of what was once the Focke-Wulf-Flugzeugbau AG engineering works, (which later became the Vereinigte Flugtechnische Werke), founded back in 1923.
When taking a tour round the works, the first station you come to is the landing flap assembly point. Landing flaps are attached to an aircraft's wings. They create more lift at low speeds such as during take-off and landing.
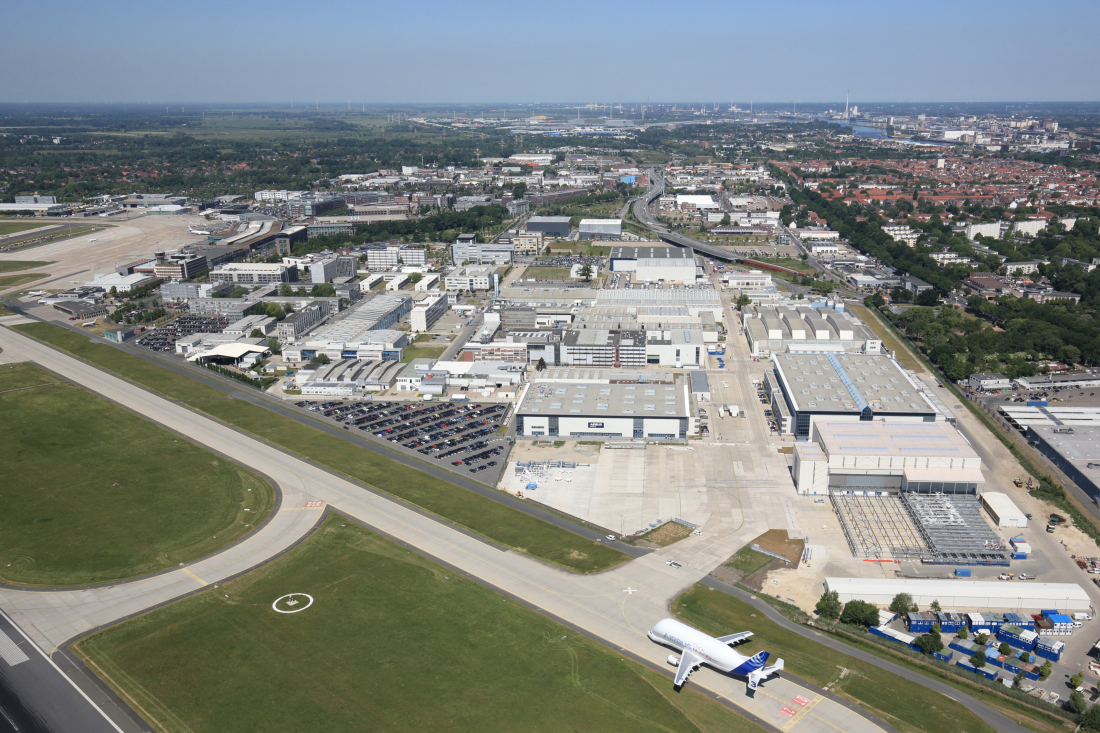
Here, the landing flaps stand next to one another in rows. In Bremen. these components are manufactured for every Airbus aircraft model. Valeska Tramp, from the Airbus communications department in Bremen, who is also joining us on the tour today, explained the manufacturing process: "Every part has its place here. We use a systematised just-in-time production process. However, some of the work steps still require true craftsmanship."
Every year, around 2,300 landing flaps of different types are manufactured in Bremen. Although the inner flap on the A320, Airbus's smallest aircraft type, is "only" 4.4 metres long and 1.2 metres wide, they can measure over ten metres on the A330. This is a huge difference which is clearly obvious, even to the naked eye. Every wing has two landing flaps, which are painted completely automatically by painting robots.
From the landing flaps to the wings at the Airbus plant in Bremen
And things get even bigger as we go through to the next hall, where the wings are fitted out. These four stations in Bremen are where the major components, hydraulic lines and several kilometres of electric cables are installed in the wings of the A330 and A350 aircraft. The blank A330 wings, weighing around 13 tonnes, arrive in Bremen from England. When they leave the Hanseatic city eight days later, bound for Toulouse, they are fully fitted out and can weigh up to seven tonnes more. Airbus's own cargo aircraft, the "Beluga", flies these fully equipped wings on to their final assembly stage. Using this process, 150 pairs of wings are built every year.
From 2025, the plant in Bremen will increasingly focus on the high-lift systems for which landing flaps are needed: Then, the majority of the manufacturing stages for the inner landing flaps for the A321 will take place in Bremen, while the wings for the A330 will be fitted out in the United Kingdom.
However, the flaps and wings are not only built and fitted out in Bremen: the Bremen site is also home to Airbus's development centre for high-lift systems. Teams of engineers and researchers are currently developing the flaps, and the drives associated with them, for the next generation of Airbus aircraft, and improving the current models.
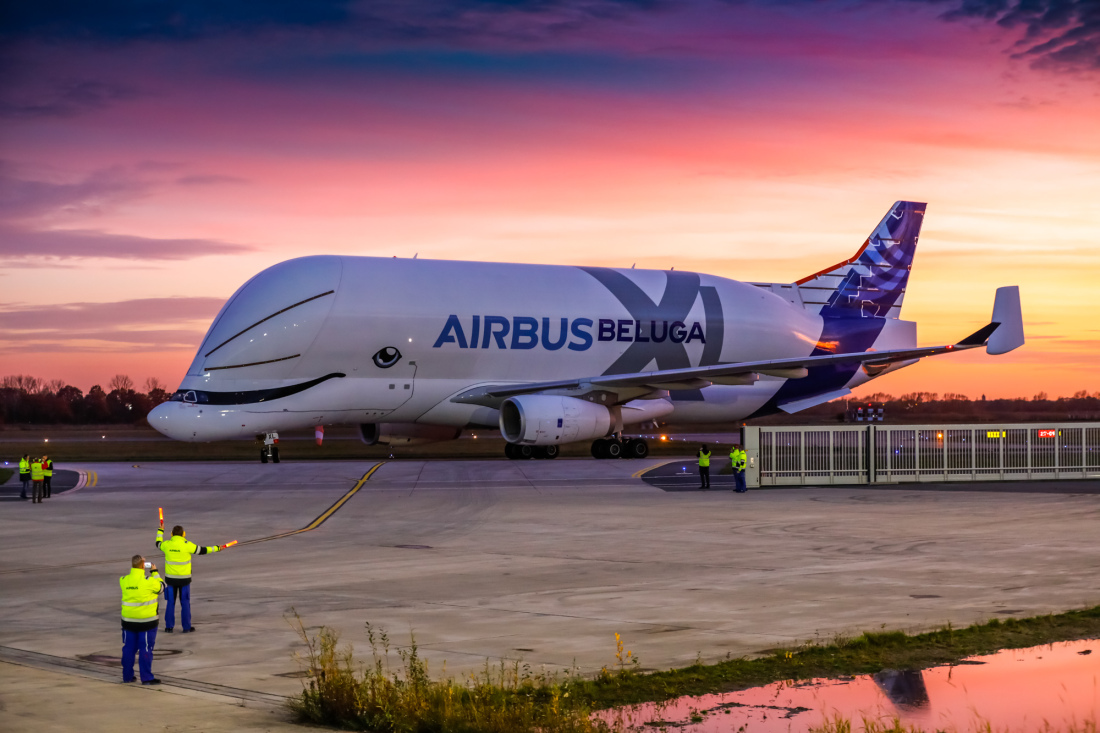
Big, bigger – A400M
On we go, into the third hall, to the A400M, Airbus's very latest military transport aircraft. The A400M's fuselage is developed and assembled in Bremen. And we're immediately confronted by the gigantic fuselage of an A400M. We ask whether there's any rivalry between the sites where the A400M is manufactured. Tramp immediately refutes the question: "All the Airbus sites complement each other. As they each have different areas of focus and expertise, they work together as a fully integrated and well-coordinated network."
The majority of the fuselage is assembled in the Hanseatic city and then fitted with various systems before it travels to Seville, in Spain, by "Beluga", for the final assembly stages. However, before this happens, the mechanics install the cargo loading system that helps the loading and unloading process run quickly and efficiently. This system was also developed in Bremen.
To date, 178 A400M aircraft have been ordered, of which 116 have already been supplied. Although production will therefore continue for a number of years to come, one of the first A400M prototypes, nicknamed "Grizzly 4", landed in Bremen in November 2022, to go into retirement after years of exhaustive test flights. In future, this transport plane will be put on display and used as an event space at the Airbus site.
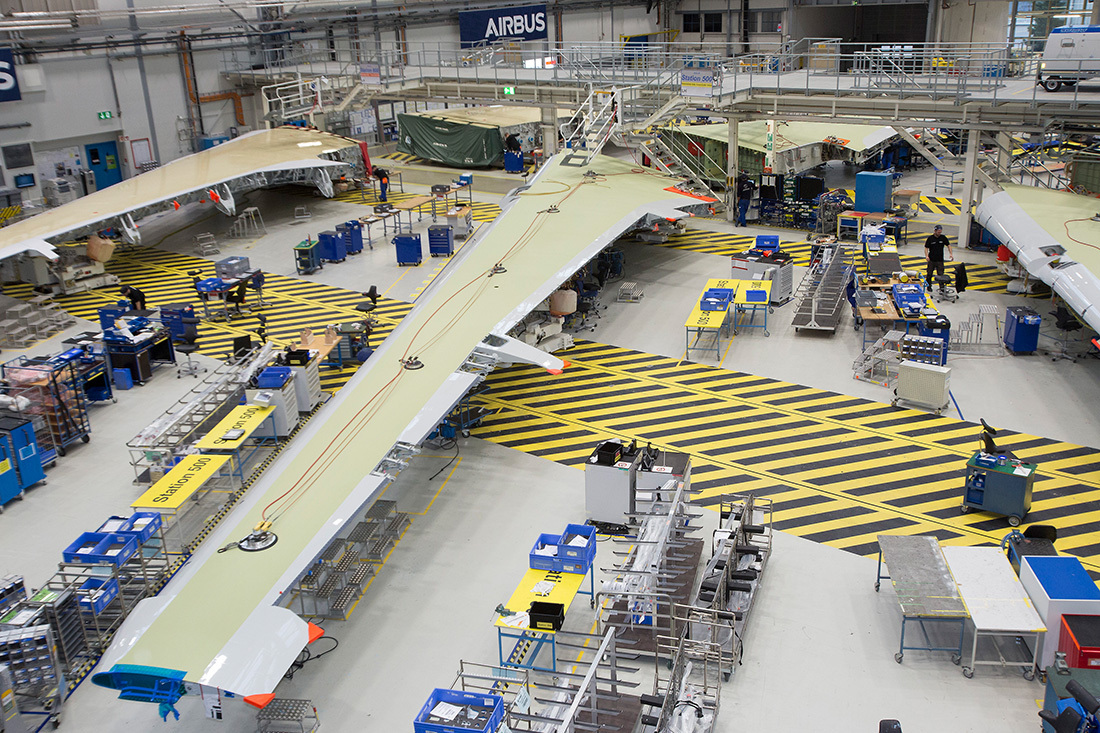
Working together to shape the future of aviation
Air travel is responsible for generating around three percent of all CO2 emissions. This will change in the coming years: climate-neutral flying is already on the starting blocks. Airbus aims to bring the first commercial aircraft powered by climate-neutral hydrogen to market by 2035. In addition, the Beluga cargo planes will be fuelled with SAF – Sustainable Aviation Fuel in Bremen.
Although this sounds like a long way off, in reality it's quite a tight schedule. This is because the new hydrogen fuel needs a completely new aircraft design and new technologies and materials, all of which must be researched, tested and given official approval.
The Bremen plant will play a vital role in this. A wealth of knowledge about tank systems, which are a critical component for hydrogen-powered aircraft, has accumulated in Bremen. Airbus has also set up one of its Zero Emission Development Centres (ZEDCs) here. This aircraft manufacturer is also an important partner for the nearby ECOMAT research and development centre.
ECOMAT, which was set up and run by Bremeninvest, is where 500 scientists from the worlds of industry and research come together to work on climate-friendly aviation, materials research, 3D-printing and digital aircraft development. Hydrogen tank systems and the new materials required for them are a focal point for a number of different research projects, as is the entire infrastructure needed for every aspect of this new fuel.
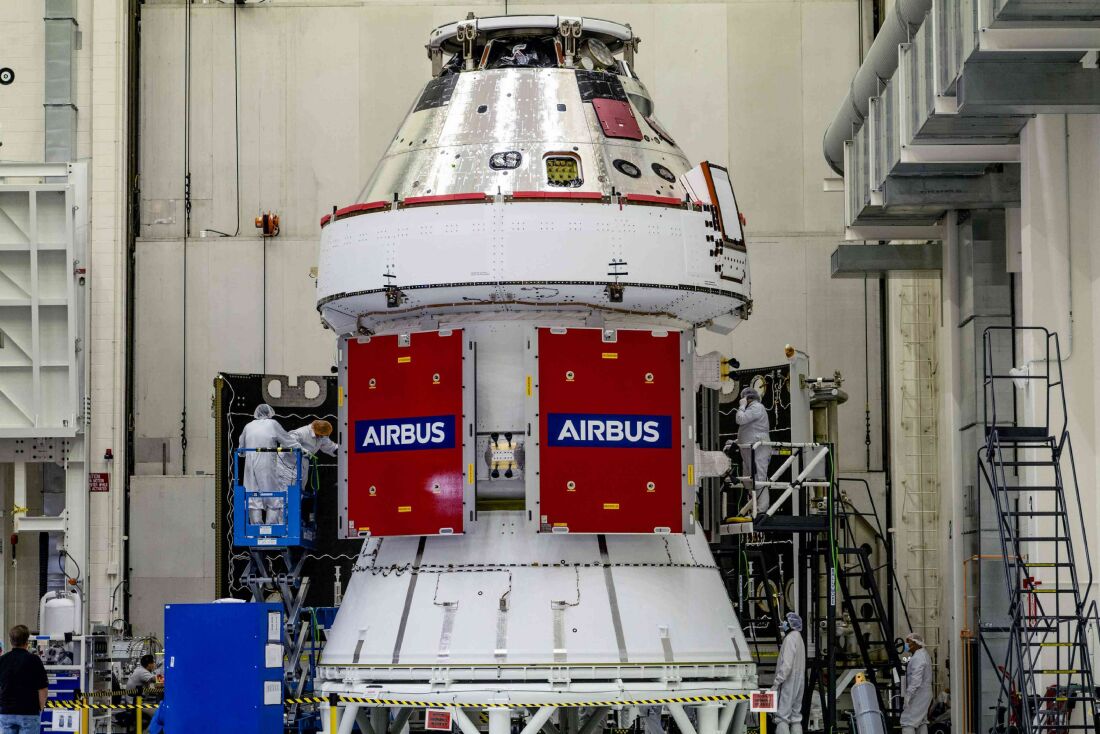
Aeronautics from Bremen
The foundations of this breadth of expertise in tank systems are close at hand, in the most literal sense. This is because Bremen's Airport City is home not only to the Airbus plant for commercial and military aircraft but also to Airbus's European competence centre for astronaut aeronautics, space robotics and the upper stages of launch vehicles. These launch vehicles are powered by hydrogen stored in tanks that are manufactured and developed in Bremen. And this is how aviation expertise moves into aeronautics, through the shortest of official channels.
Around 1,000 of Airbus's 4,500 employees in Bremen work in the Defence and Space sector. Added to them are the staff at the local ArianeGroup plant, a joint venture in which Airbus is also a participant. Every Ariane rocket starts its journey into space with an upper stage that is made in Bremen. NASA's new moon mission – Artemis – also successfully made its maiden flight in December 2022, fitted with a service module from the Bremen plant. Not only that, but the Columbus space laboratory in the International Space Station and all the station's European parts that were made in the Hanseatic city, are also managed from here.
Once again, the upper stages of the new Ariane 6 rocket, whose first launch date is scheduled for the end of 2023, will be supplied from the city on the River Weser.
Testing and repair
The Airbus facility in Bremen also houses the Testia subsidiary which specialises in materials testing and training of test engineers. After all, the motto is: safety first. The company is a partner in ECOMAT and participates in research projects such as those for enabling tests to be performed using artificial intelligence.
And last but not least: Far away from the factory site, in the Stuhrbaum industrial estate at the gates of Bremen, is the group's European repair centre. This isn't where entire aircraft come when they need to be repaired, but is where individual components, such as the landing flaps, are sent for servicing.
It's clear to see that Airbus is the focal point of the European aerospace industry and that Bremen, as one of the major locations, plays a central role in this. All the many interdisciplinary research projects running here are the foundations for many more aircraft and space vehicles in the coming decades.
Success Stories
How a space enthusiast campaigns for women in STEM fiels and Bremen as a space location
How does someone from a small village in Poland end up working on human spaceflight in Bremen? Dr. Anna Chrobry shares her journey through science, passion, and perseverance—and explains why she proudly calls herself a "space girl."
Learn moreVisions for the future of aerospace
From car navigation systems to weather reports - hardly anything works without satellites. They need fuel, but this is often toxic. The Institute of Aerospace Technology at Bremen University of Applied Sciences is researching environmentally friendly alternatives. What the future of space travel could look like.
Learn moreTake-off for Bremen: what makes the city a hub for aerospace expertise
The sky is not the limit. Science, production, development and business all agree on this. Aircraft wings, Ariane rockets, Galileo satellites - Bremen is one of the top locations in the international aerospace industry. Five reasons for Bremen's success story.
Learn more