Schlank, individuell, intelligent – das sind die Traummaße der Fabrik der Zukunft
Digitalisierung / Industrie 4.0Interview zur Digitalisierung in der Fertigung
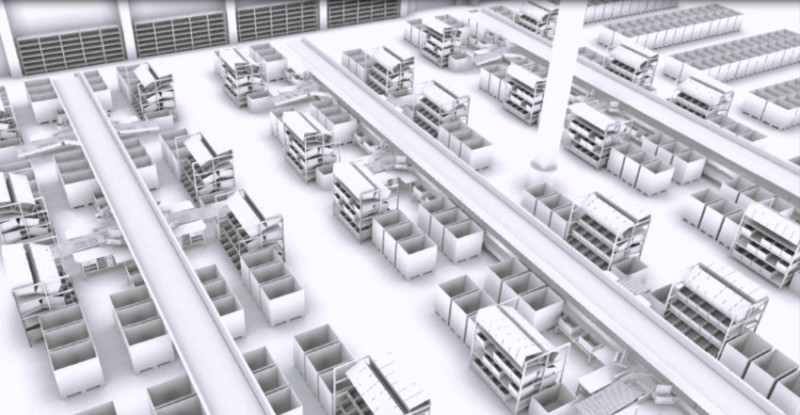
Dr. Jörn E. Fischer ist Prokurist, Bernd Kidler Senior Consultant bei der GPS Planfabrik in Bremen. Zusammen mit ihren 13 Kollegen entwickeln und planen die beiden Experten Fabriken und Logistikzentren in ganz Deutschland. Eine Aufgabe, die durch Industrie 4.0 komplexer geworden ist. Denn wer heute seine Produktion erneuert oder erweitert, sollte jetzt schon die Voraussetzungen für eine digitalisierte Fabrikation schaffen, selbst, wenn noch keine konkreten Maßnahmen geplant sind. Davon sind Fischer und Kidler überzeugt.
Herr Fischer, Herr Kidler, was heißt für Sie in diesem Zusammenhang „Industrie 4.0“?
Dr. Jörn E. Fischer: Bei Industrie 4.0 geht es um die Reduktion von Komplexität, um weniger Steuerungsaufwand und die Verringerung des Bestands, darum, die Fertigung flexibler und effizienter zu gestalten. Maschinen müssen als autonome Einheiten begriffen werden, die selbstständig Entscheidungen treffen können, die weniger zentrale Planung benötigt.
Industrie 4.0 ist in Theorie eine Revolution, in der Praxis ist dieser Prozess eher eine Evolution.
Dr. Jörn E. Fischer
Bernd Kidler: „Industrie 4.0“ wird häufig auf Technologien wie Breitband, cyber-physische Systeme, Big Data reduziert. Für uns stellt sich die Digitalisierung hingegen als Instrumentarium dar, um bessere und effizientere Geschäftsprozesse über Unternehmensgrenzen hinweg mit dem Ziel einer individuellen und flexiblen Fertigung zu realisieren. Industrie 4.0 ist in Theorie eine Revolution, in der Praxis ist dieser Prozess eher eine Evolution.
Die GPS Planfabrik plant Produktion und Logistik und berät Unternehmen in der Umsetzung. Sie müssen daher die Zukunft der Fabrik ganz genau kennen, um ihre Kunden vorzubereiten. Wie sieht die Fabrik der Zukunft aus?
Dr. Jörn E. Fischer: Die Fertigung der Zukunft wird eine „Fabrik in der Fabrik“ sein. Es gibt einen Trend zur Segmentierung, Produktionseinheiten werden kleiner und autonomer. Statt einer Fertigungslinie wird es verschiedene, kleinere Linien geben, die flexibler und wandelbarer sind. Das stellt hohe Anforderungen an die Maschinen und das Gebäude selbst, die durch Industrie 4.0-Prozesse adressiert werden können. Ziel ist die Steigerung der Effizienz, der Wandlungsfähigkeit und der Produktionsgeschwindigkeit.
Bernd Kidler: Der große Treiber ist die steigende Varianz, die zunehmende Frage nach individuelleren und vielfältigeren Produkten. In den kommenden Jahren wird sich der Trend zu kleineren Losgrößen massiv verstärken. Und die Anforderungen an die Fertigung werden immer mehr von direkten Kundenwünschen getrieben werden. Eine Fertigung, die darauf vorbereitet sein will, muss nach dem „Lean Management“-Prinzip aufgebaut sein – sie muss auf alles verzichten, was nicht unbedingt auf die Zielerreichung ausgelegt ist. Es geht immer um den optimalen Materialfluss.
Es geht immer um den optimalen Materialfluss.
Bernd Kidler
Welche Schritte müssen folgen, um die Digitalisierung in der Fabrikpraxis umzusetzen?
Dr. Jörn E. Fischer: Auf dem Weg zur Smart Factory müssen wir zwei Stränge verfolgen. Zum einen den Materialfluss weiter optimieren. Das heißt: Kurze Wege, alle Prozesse sind dicht beieinander und werden lokal – also dezentral – gesteuert. Jede einzelne Produktgruppe hat idealerweise einen Supply Chain Manager, also einen Hautverantwortlichen für das jeweilige Produkt. Damit bewegen wir uns weg von der klassischen Abteilungsstruktur in Unternehmen, denn der Supply Chain Manager kann auf alle Prozesse zugreifen – auf Einkauf, Lagerhaltung, Produktion und Versand.
Dies führt uns gleich zum zweiten Strang – die Komplexität zu senken und die Flexibilität zu erhöhen. Die Produktion heute hat entweder Serien- oder Manufaktur-Charakter. Die Fabrik der Zukunft muss deutlich flexibler auf Bedarfsänderungen reagieren können. Ziel ist die Produktion hoher und niedrige Stückzahlen – bis zur Losgröße 1 – mit nahezu gleicher Effizienz. Mit Hilfe kleineren Produktionssegmenten, neuen Automationstechniken, vermehrten Roboter-/Mensch-Interaktionen, additiven Fertigungsverfahren wie dem 3D-Druck und dem so genannten cyber-physischen Produktionssystem lässt sich dieses Ziel zukünftig einfacher erreichen.
Bernd Kidler: Man muss zudem eines herausstellen: Das große Potenzial der „Smart Factory“ offenbart sich erst im Netzwerk mit anderen Smart Factories, wenn Daten von verschiedenen Unternehmen gemeinsam genutzt werden können. Wenn zum Beispiel die Kunden auf die Produktionsdaten beim Hersteller zugreifen können, um nicht nur den Status ihres Auftrags einzusehen, sondern aktiv bis unmittelbar vor Fertigungsbeginn noch ihre Sonderwünsche elektronisch einstellen können. Aber hier gibt es heute noch große Hürden und Bedenken, gerade auch aus dem Mittelstand. Einmal in der Standardisierung, denn heute weiß noch niemand, welche Schnittstelle und welche Technologie sich durchsetzen werden. Da will niemand auf das falsche Pferd setzen. Und zum anderen in der Datensicherheit. Hier gibt es große Ängste davor, mit den Informationen auch wichtige interne Daten über das Unternehmen an Dritte weiterzugeben.
Steht sich der Mittelstand da selbst im Weg und verschläft so eine wichtige Entwicklung, während Unternehmen aus anderen Ländern vorbeiziehen?
Bernd Kidler: Unter den heute bestehenden Randbedingungen wird wohl kaum ein Unternehmen beschließen, die eigene Fertigung komplett und in einem Zuge auf „Industrie 4.0“ umzustellen. Stehen aber Veränderungen beispielsweise durch Ausweitung der Produktion oder Hinzunahme einer weiteren Produktlinie an, sollte man heute eine „Industrie 4.0“ konforme Umsetzung sehr ernsthaft ins Kalkül ziehen. Wir achten jedenfalls immer auf die Umsetzung der Grundvoraussetzung für Industrie 4.0 konforme Prozesse, die Modularisierung der Informations- und vor allem der Materialströme. Steht sich der Mittelstand im Wege? Nein, aber jede Veränderung muss sich schlicht rechnen. Und das gilt auch im internationalen Vergleich.
Welchen Weg muss der Mittelstand dann gehen?
Dr. Jörn E. Fischer: Wir empfehlen grundsätzlich ein Stufenmodell, denn die „Digitalisierung in einem Rutsch“, können sich die meisten Unternehmen nicht leisten. Zunächst fangen Mittelständler bei der Optimierung der eigenen Prozesse an, am besten zunächst in Teil- und Pilotprojekten, auch in Zusammenarbeit mit externen Beratungen wie der GPS Planfabrik. Dann sucht man gemeinsam nach geeigneten Umsetzungen und Technologien, um so Schritt für Schritt voranzuschreiten. Denn abwarten bis alle Eigenheiten erprobt und kostengünstig verfügbar sind, wäre ein fataler Weg.
Abwarten, bis alle Eigenheiten von Industrie 4.0 erprobt und kostengünstig verfügbar sind, wäre ein fataler Weg.
Dr. Jörn E. Fischer
Bernd Kidler: Man muss zuerst die richtigen Voraussetzungen schaffen. Zunächst einmal müssen Unternehmen sich darauf verständigen, was sie mit Industrie 4.0 eigentlich genau meinen: Reden sie von der vollständigen Digitalisierung der Geschäftsprozesse? Oder meinen sie erstmal nur die Datenerfassung der Maschinen? Erst wenn man über dasselbe spricht, kann man im nächsten Schritt sich die Prozesse im Unternehmen anschauen und fragen: Wo können wir optimieren? Von welchem Niveau aus starten wir? Hier setzen wir mit der Initialberatung von GPS häufig an. Aus dieser Betrachtung kann man dann Ziele definieren – eine Vision schaffen, mit der dann alle anderen Schritte bis hin zu konkreten Umsetzung unternommen werden können. Also die Umstellung der Fertigung, der Prozesse und Weiterbildung des Personals.
Gerade das Thema Personal – Arbeit 4.0 – steht immer stärker auf der Agenda, gerade auch bei der Bundesregierung. Welche Bedeutung hat die Vorbereitung der Arbeitskräfte und der Wandel des Arbeitens bei Unternehmen?
Dr. Jörn E. Fischer: Die Auswirkungen von Industrie 4.0 auf das Personal, die Belegschaft, sind noch kaum ein Thema für Unternehmen. Das steht hinten in der Priorität. Zurzeit sind Unternehmen noch damit beschäftigt, die physikalischen Voraussetzungen zu schaffen – sich damit zu beschäftigen, wie Fabriken für Industrie 4.0 vorbereitet werden müssen, welche neuen Maschinen angeschafft werden müssen. Der darauffolgende Schritt ist dann die Digitalisierung der Prozesse. Erst dann kommt das Thema Schulung und Fortbildung des Personals.
Kommen Unternehmen mit konkreten Industrie 4.0-Fragestellungen auf Sie zu?
Dr. Jörn E. Fischer: Nur selten. Unternehmen treten meistens an uns heran, wenn Sie ganz konkret die Effizienz erhöhen, Strukturen verändern und Kosten senken wollen. Das sind die primären Interessen. Noch ist der Druck vom Markt gering, in vielen Bereichen gibt es noch große Fragezeichen und Unklarheiten bezüglich der Digitalisierung und der Datensicherheit. Aber natürlich sind bei der Planung von Fabriken bzw. bei der Optimierung von Produktion und Logistik die Möglichkeiten, die Industrie 4.0 bieten wird, bereits heute zu berücksichtigen. Man darf sich nichts verbauen. Und genau da kommt die GPS Planfabrik ins Spiel.
Herr Dr. Fischer, Herr Kidler, vielen Dank für das Gespräch.
Zum Unternehmensprofil der GPS Planfabrik auf der Plattform Industrie 4.0 Bremen
Welche Services die WFB Wirtschaftsförderung Bremen GmbH bei der Digitalisierung ihres Unternehmens bietet, finden Sie auf der Übersichtsseite Digitalisierung.
Erfolgsgeschichten
14 KI-Unternehmen in Bremen
KI-Unternehmen profitieren in Bremen von einem starken Netzwerk, gut ausgebildeten Fachkräften und einem wachsenden Forschungs- und Wirtschaftsumfeld. 14 Unternehmen, die zeigen, dass KI mehr ist als ChatGPT.
zu Bremen-InnovativWie Bremer Unternehmer vom Silicon Valley lernen
Vier Bremer Unternehmen berichten, was sie aus einer gemeinsamen Reise über den großen Teich mitnehmen. Geht es in Bremer Büros also schon bald etwas amerikanischer zu?
Mehr erfahrenVom Insektenbein bis zum Beton – neues Mikroskop macht Verborgenes sichtbar
Wie verhalten sich Materialien im Nanometer-Bereich? Das neue ESE-Mikroskop an der Hochschule Bremen erlaubt erstmals hochauflösende Einblicke auch für die Materialforschung in der Luft- und Raumfahrt.
zum ECOMAT