What does Industry 4.0 mean? The definition of digitization
DigitizationDigitalisation defined in just a few words
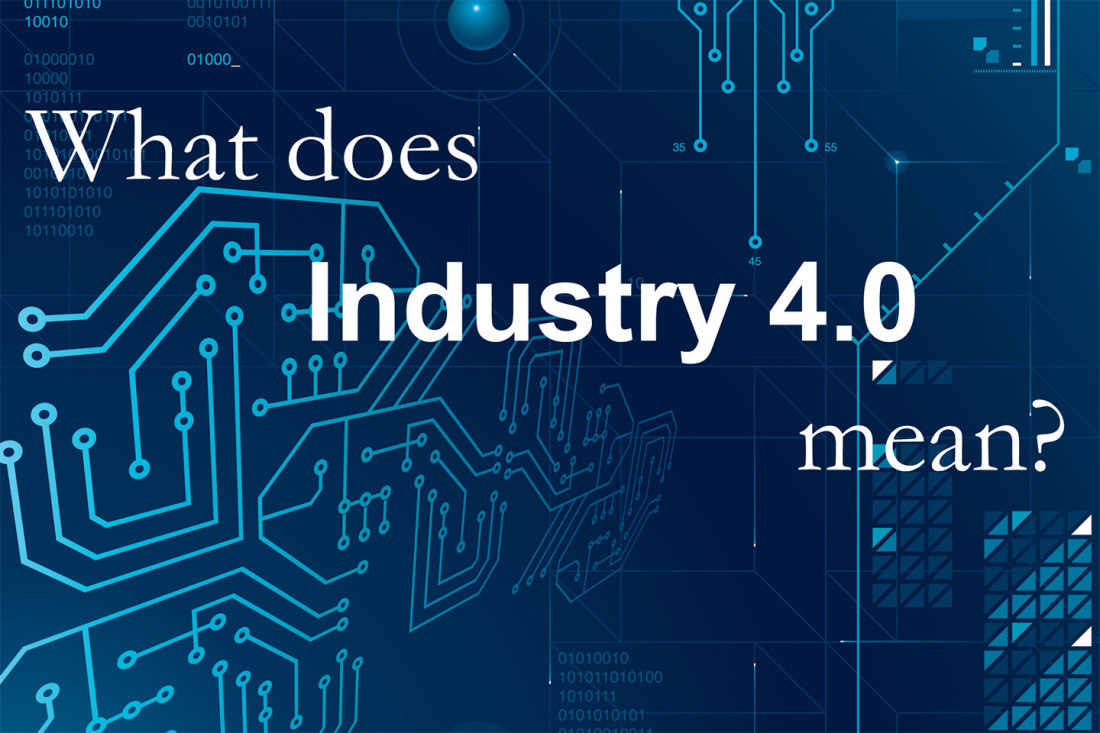
What does Industry 4.0 mean? Industry 4.0 refers to the digitization of manufacturing. So much for the definition. Digitalisation describes the increasing use of networked, web-enabled and automated technologies in our society. Industry 4.0 specifically refers to the development in industry, for example in vehicle construction, engineering and transport.
Two developments are at the heart of Industry 4.0: connectivity and decentralised control. Networked systems facilitate the exchange of data and therefore of information, making it possible for them to react intelligently to one another.
The concept of autonomy is totally different to the established practice of managing machines centrally. Currently, information from a wide range of IT systems is collated and evaluated by people, who then make the necessary adjustments – to increase the rate of production or to manufacture goods more efficiently, for example.
Industry 4.0 will fundamentally change this process. In the digitalised future, all machines and the goods they produce will be fitted with sensors. These will enable them to optimize their processes and continually communicate not only with each other but also with other systems. Production, distribution, development and even customers and suppliers will be incorporated into the networked world.
The term Industry 4.0 in its current form was coined by a subcommittee of ‘Forschungsunion Wirtschaft – Wissenschaft’ whose recommendations, published on 25 January 2011, included a project called Industrie 4.0 with a focus on future technology. ‘Forschungsunion Wirtschaft – Wissenschaft’ was a committee of experts who, from 2006 to 2013, advised the federal government on strategies for establishing Germany as a high-tech hub. It was made up of representatives from science, business and industry. Since then, Industry 4.0 stands synonymously for the digitization of the manufacturing industry.
Smart control is a characteristic of Industry 4.0
Networked machines control themselves autonomously and intelligently. Each machine knows how many parts there are left in the warehouse, and if stock is running low, the system automatically sends a request to the supplier to send more. Some machines can plan production processes autonomously and at lightning speed. For example, if a buyer decides at the last minute that his car should have a sun roof, the factory automatically plans another route through production for this vehicle.
The move from central control to decentralised, autonomous optimisation is the next step towards the smart factory. Robots and machines are no longer mere automatons that repeat one work step a million times. The networking of all production processes means that they decide autonomously which component takes which route through production. As a result, logistics processes within companies, but also across supply chains, are becoming leaner.
The internet is the key to digitalisation
Each component must be digitally captured to enable it to communicate with others. Sensors in machinery and digital technologies such as RFID chips are paving the way for Industry 4.0. The Internet of Things (IoT) is what we call the fitting of sensors to all items and the creation of digital information paths for processes. Communication across boundaries, be it between person and machine, production equipment and inventory, or company and customer, takes place via the internet. This type of communication requires a fast and powerful mobile phone network, recently launched as 5G.
This next-generation wireless network standard is of particular interest to industry. There are also other ways of transmitting and collating data wirelessly, such as Low Power Wide Area Networks (LPWAN), one of which is currently being tested at Bremen steel works.
A digital twin simplifies processes
All processes in a company – whether factories or logistics chains – can be digitally reproduced from this data and turned into digital twins. These virtual copies of real-world processes have a number of benefits. They allow you not only to see all currently running processes at a glance but also to virtually make changes to production or the transport chain and then run a simulation. As a result, optimisations can be checked more quickly, faults and errors in planning can be identified more cost-effectively, and time and money can be saved.
Digitalisation means connectivity beyond boundaries
Connectivity, or digitalisation, is not limited to the shop floor, i.e. the factory hall or the shipping warehouse. If manufacturing is digitalised, then the processes behind it need to be too. And not just within your own company, but also at your suppliers, customers and end users. Such end-to-end connectivity can achieve significant efficiency gains.
Collecting and processing data is part of this. Companies with data-driven business models such as Google and Facebook are among the world’s most valuable businesses, as they have found a way of monetising huge volumes of data. Industrial companies have access to a huge wealth of data too, and evaluating it is an important process within Industry 4.0. Big data and artificial intelligence (AI) (german) are key terms in this respect. But rather than the user data of customers or suppliers, it is more about production and process data. The potential of artificial intelligence in this area, in particular, is hugely underestimated. AI is able to collect and evaluate data in a way that previously would not have seemed even remotely possible. To give an example: as a paper clip manufacturer, would you be able to check every single clip for defects using a photo? AI can. As a freight company, could you track every route of every truck and optimise it in real time? AI can do that too.
Maintaining and evaluating data also makes new business models possible in the service sector. The ability to collect data even long after a machine has been delivered to the customer, for example, makes it possible to sell servicing contracts with real-time monitoring and optimisation. This can help to bind the customer even more closely to the manufacturer.
Robot-based automation, web-enabled machines, AI, big data – many of these have been around for some time. What makes Industry 4.0 different is that information is available from across the company, and processing it is more efficient. Increasingly, stand-alone solutions are giving way to connected systems.
Industry 4.0 is paving the way for efficient manufacturing in the future
But what is the point of it all? What is driving the digital transformation? The simple answer is: we are. Consumers are increasingly demanding customised, rather than off-the-shelf, products. Even one-offs are no longer that unusual. Vehicle configurations are a good example. It is already possible to put together the car of your dreams, with model, colour, engine type, equipment level and optional extras just some of the choices available. This results in millions of potential configurations, some of which might be the only one of its kind in the world.
A product tailored to the customer’s wishes requires tailored manufacturing. But made by hand? Not at all. Intelligent manufacturing is the answer. Producing bespoke items en masse is only possible if the factory is capable of manufacturing one-offs, i.e. it can decide for each component which route to take and which piece of machinery will work on it. This puts the focus on the customer more than ever before. Customer-focused solutions are at the heart of the new production environment, and companies must adapt to this. Not only at the production level, but above all in product design, marketing and sales.
The factory of the future can react rapidly and flexibly, allowing it to increase efficiency and manufacture according to actual demand. No human would be capable of changing plans as quickly and process so much information from so many different sources while still making the best possible decision. Machines, some equipped with artificial intelligence, can take over this task and open up completely new possibilities that we would never have seen before.
One of these possibilities is 3D printing. This may still be in its infancy, but the progress it has made is impressive. In fact, the first 3D-printed parts to be fitted in airplanes will be taking to the skies soon. This technology is essentially the apex of bespoke production – every 3D-printed part can look different and meet a different specification. Not everything will be made by 3D printer, of course, as bespoke parts will remain more expensive than mass-produced items in the long run. But they are a viable alternative for special requirements and individual requests.
Much will depend on how well you know your customers and how well you can cater to their needs. Customer focus is one of the key drivers behind the digitalisation of processes. Companies must ask themselves how they can use new technologies to better serve their customers’ requirements – or even to find out about them in the first place.
Work 4.0: the way we work is also changing
This development is not confined to the factory floor. Digitalisation is creating new business processes in many areas, and companies will have to adapt their administration, sales and marketing accordingly. Industry 4.0 is influencing the way we work, and that presents considerable challenges for companies. So what does Industry 4.0 mean for labour?
On the one hand, ever-greater connectivity and automation are replacing jobs with robots, artificial intelligence and new machines. On the other, more and more is expected of highly qualified personnel, and there is growing demand for them on the labour markets. New jobs are being created by digitalisation and the new business models it makes possible. People have more time for important things: routine tasks are handled by machines, while employees can concentrate on interpersonal matters, planning, organising and creative thinking. Movements such as New Work are examining what this new world of work might look like, and are considering questions such as: what will our work look like in the future?
The onus is on companies to pick up on this trend in good time, especially given the high demand for suitably qualified employees. Knowledge work is likely to be a key factor in value creation in the future, and a growing number of companies are taking the decision to establish their own development departments. In order to fully exploit the potential offered by digitalisation, employees will need to be given the motivation and skills to cope with the new processes.
The opportunities offered by Industry 4.0
Digitalisation will not have the same impact on every company. While many businesses are already unable to work without digital services, other processes are so complex that it will be some time before machines can handle them. But sooner or later, the digital transformation will affect everyone, and only those who embrace it early on will have a good chance of surviving.
Digitalisation does not always have to be technically demanding. A builder may not need digitalised machines and artificial intelligence on the building site, but an app that makes it easier to coordinate appointments with customers or reorder materials might be very welcome. And that is digitalisation too.
If you embrace the opportunities presented by digitalisation, you will increase your production efficiency and gain a competitive edge in the market. This will allow you to offer your customers benefits that your competitors can’t. In industrial companies, these could be remote maintenance via the internet, for example, or the use of data to analyse failure rates and thus predict maintenance measures. Who wouldn’t like to know when their machines might break down before they actually do?
Do not tackle digitalisation on your own
Companies today face many challenges when it comes to the digital transformation, and the best way to overcome them is with the help of a strong partner. Collaborative relationships, networks and trade associations, such as the German government’s Mittelstand 4.0-Kompetenzzentren (SME 4.0 centres of excellence), can unlock levels of potential that may be difficult to manage on your own. While large companies can afford to run their own development departments and experimental projects, SMEs find it more difficult to free up time and resources for projects with an uncertain outcome. Joining forces with a knowledgeable partner can reduce the pressure. Potential partners include universities and research institutes, but also suppliers and customers.
What does Industry 4.0 mean? A summary
The main challenges facing companies today are:
- Standardisation of interfaces: Companies usually run a wide range of different software, and rarely are they compatible with each other. Yet a system’s ability to communicate with other systems is a prerequisite of Industry 4.0.
- IT security: All too often, the media report data leaks, highlighting the fact that the Internet of Things only really makes sense if data can be stored and exchanged securely online.
- Human-robot communication: Robotics has huge potential, but has so far been restricted to a limited range of tasks. If people and robots can safely work side by side, their use will become more widespread.
- From customised production to one-offs: Customised production requires customised marketing, sales and business processes. Industry 4.0 transforms the entire company, not just the machines in the factory.
- Autonomous processes in flexible factories: Industry 4.0 does not necessarily equal new machines. With a little creativity, many old machines can be made fit for the digital age.
- Big data and AI – data analysis provides process optimisation: Collecting data is easy, but it takes highly skilled specialists to draw useful conclusions from it.
- Work and training in the digital age: How will we organise work in the future if robots and AI will be carrying out part of it? What will there be left for us to do? It is important to consider these questions early on.
- Customer-centred thinking: The customer must always be at the heart of every consideration. What does the customer want? How can digitalisation help to achieve it?
Industry 4.0 has many facets, and at first glance it looks more complex than it actually is. The best advice is to start by picking out one aspect and getting interested employees on board to contribute and implement new ideas. There is no right or wrong way of doing things, and every company has to find its own path. After all, every company is different.
The definition of digitalisation has evolved over time
Industry 4.0 is often referred to as the fourth industrial revolution, as it represents a completely new way of organising work and production. To find out why this is and what lies behind the term ‘digital transformation’, read our history of digitalisation (german).
Success Stories
“After all, we're here because someone else made room for us, and it's our duty to do the same for others”
Theoretical physicist, industrial mathematician, manager – as a member of the start-up company TOPAS, Dr. Shruti Patel creates change in Bremen. However, being a role model has not always been easy for her.
Learn more12 Examples of AI in Medicine and the Health Sector
Detecting cancer earlier or avoiding accidents at work - AI will make our lives easier and easier in the healthcare sector. In Bremen, a strong AI landscape is developing in the healthcare sector, as these 12 examples show.
Learn moreThese Bremen companies are developing autonomous systems
Self-driving cars, drones, robots - in Bremen, autonomous systems are a focus of numerous focus of numerous companies. A look at the diverse corporate landscape and where the committed players can be found.
Learn more