There is No Machine like This One in the World – and It Comes from Bremen
Investing in BremenTitanium alloys for the aviation, aerospace, medicine, automotive and mechanical engineering sectors
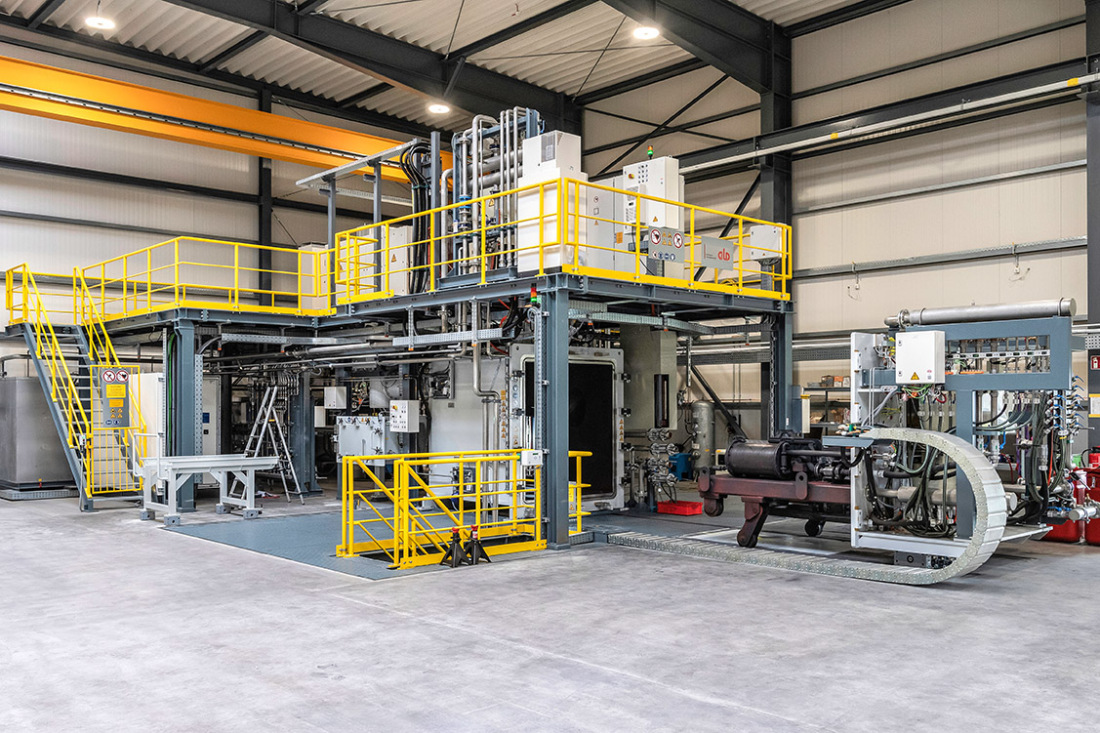
As a raw material, titanium is in great demand world-wide. Industries such as aviation, aerospace, medical, automotive and mechanical engineering are all major users of this lightweight alloy. Only a few companies in the entire world deal in intermediate or semi-finished products made of titanium. One of these companies comes from Bremen.
The trade in raw materials is worth billions. Nowadays, every step in the process chain, from mining to metal production to the wholesale trade, is controlled by company groups. Anyone visiting Bremen, and the Bremen Industrial Park industrial estate in particular, will find immediate proof of this. This is because the ArcelorMittal steel works, where millions of tonnes of steel are produced every year, is located right next to the northern part of this industrial estate. The rust red towers of the smelting furnaces spiral up 100 metres into the air, emitting a constant stream of smoke and steam from the rolling mills.
No room for the little guys? Far from it! The company HWH (Hanseatische Waren Handelsgesellschaft) is based close by, in the same industrial estate. The name has a global reputation for reliability in the titanium trade, and has all kinds of specialist knowledge about this valuable lightweight alloy.
"We occupy a niche in the market. We handle special orders and supply customer-specific metals and semi-finished products world-wide in batches that are too small to be of interest to the big companies. This is what makes us so special", explained Dr. Patrick Voigt from HWH. The company's warehouses in Bremen hold round bars, flat bars, wire rod and cast ingots. There, components for the automotive sector, and also the intermediate materials used in dentistry, are created.
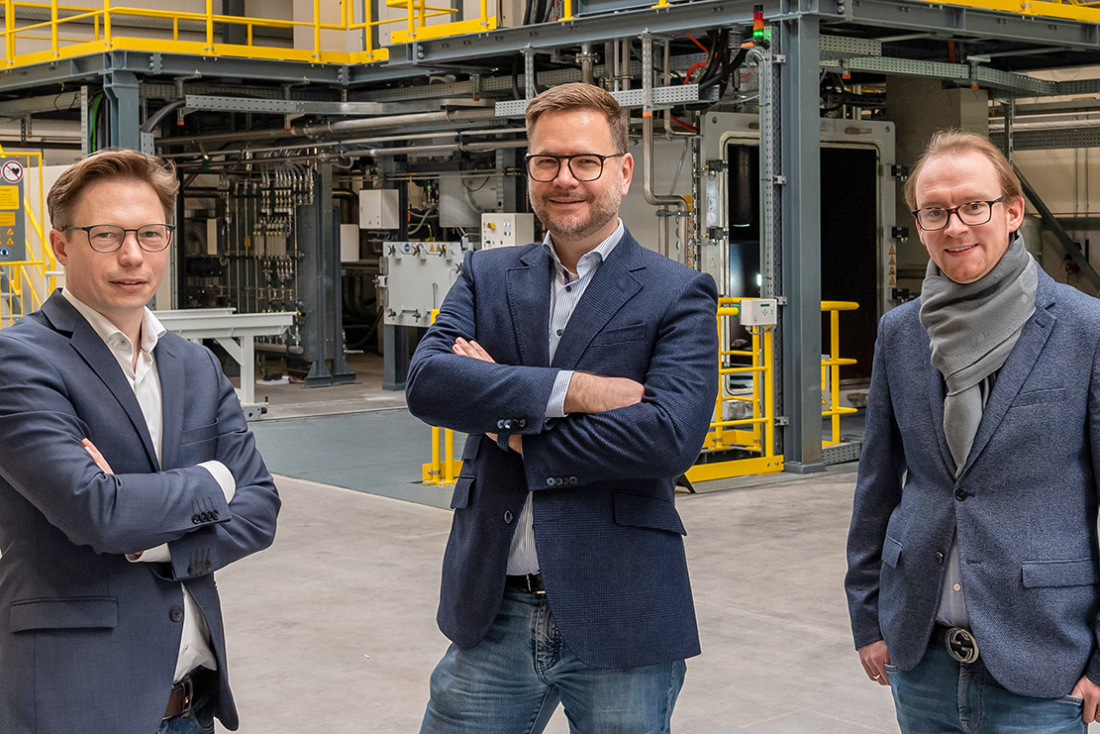
Titanium smelting plant heralds a change to the company
However, Voigt isn't here to talk about the trading business. This Bremen company is already an established player in this field. The Director of Development & Production is much more interested in the new production hall that has been erected on the company site over the last four years.
This hall houses the new plasma-hybrid smelter: a two-story smelter occupying a large part of the building, with a footprint similar to a 4 room apartment. It marks the start of a new chapter in the history of HWH. This trading company is evolving into a manufacturer with an expertise in production that can be found nowhere else in the world.
Titanium alloys: specialist knowledge required
This plant will smelt thumbnail-sized pellets of titanium and other metals to create alloys. Alloys are compounds made up of two or more metals. When melted together at high temperatures, these metals take on new properties. Every compound contains different ingredients, much in the same way as a cooking recipe: in Bremen, aluminium, niobium, boron or molybdenum can be added to the titanium. "We are able to produce bespoke alloys for customers, on request. And we can supply them in batches ranging from just a few kilogrammes to large-scale production runs that involve several tonnes of material", explained Voigt proudly looking over at the new smelter.
At the heart of the smelting plant is the melting chamber where a plasma lance generates a peak temperature of 5,000 degrees to liquify the metal mixture within a protective atmosphere. The hybrid process used to operate the melting chamber was developed in-house by HWH. The smelting and subsequent solidification process can be controlled with great precision, not only optimising the quality of the alloy but also ensuring that the plant runs as efficiently as possible.
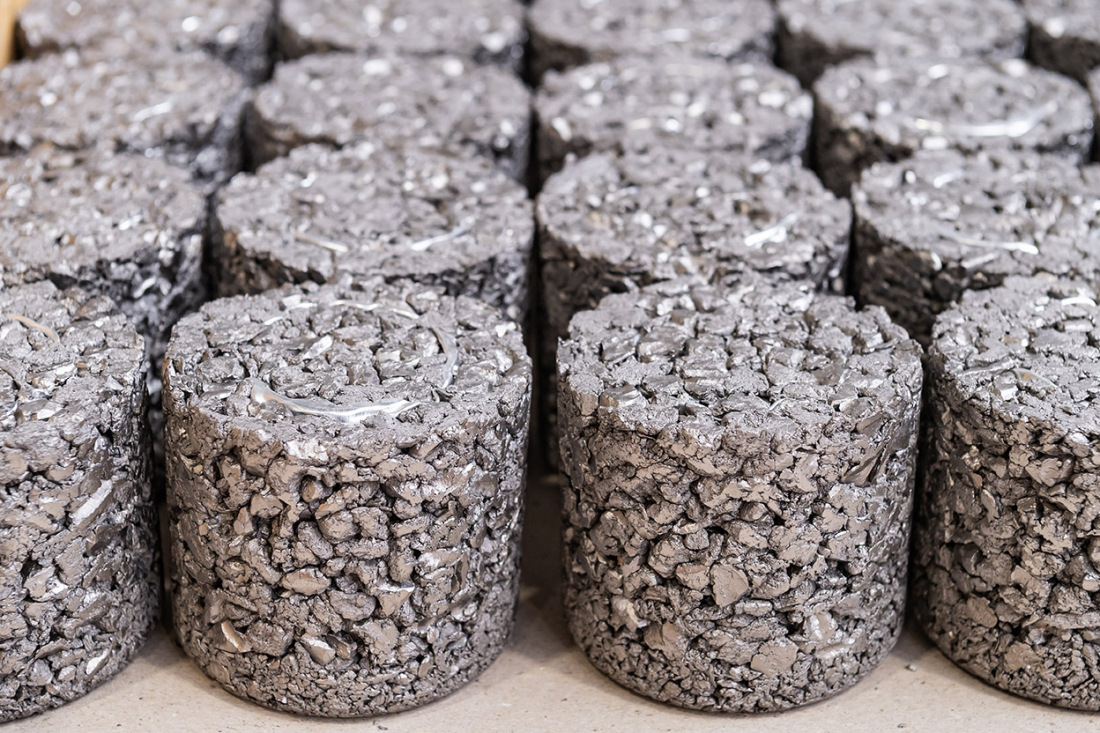
Innovation from Bremen fills a gap in the market
The process creates a thick metal ingot which, depending on the specification, can be between 7 and 24 cm in diameter and up to two metres long. HWH's customers can then use these ingots to manufacture their products, some of which have quite astounding properties: for example, there are titanium aluminides used in aviation, refractive metals for high temperature applications, hydrogen storage alloys that can bind this volatile gas, superconductive materials or shape memory alloys which always take on the same shape at particular temperatures.
This Bremen company also produces metals for additive manufacturing processes. Other service providers then transform these metals into the powders used in 3D printing. "We are well equipped for the future", summed up Marc Reimer, Sales Manager at HWH. "Companies in the processing industry find it very hard to source these special alloys because there are so very few manufacturers that produce them. With our smelter, we can fill this gap in the market. As a medium-sized company, we are also extremely agile. All this means that we have virtually no competition, anywhere in the world". The new smelting plant can produce 100 tonnes of alloys per year.
A gamble pays off
When the plant officially came into operation, at the turn of 2021/2022, the engineers felt that a weight had been lifted off their shoulders. Researching this innovative new smelting process and investing in the machines and production hall had been a real commercial challenge for this medium-sized company and its 20 employees. "It has taken us about 10 years to develop this process. We always had faith in this idea and were sure we could establish a new area of expertise for our future. However, it also cost us all a great deal of time and effort", remembered Daniel Hempel, Business Administrator at HWH.
The company developed the first prototype in a research project. "After that, we were able to finalise our design ideas with the help of a well-known mechanical engineering company."
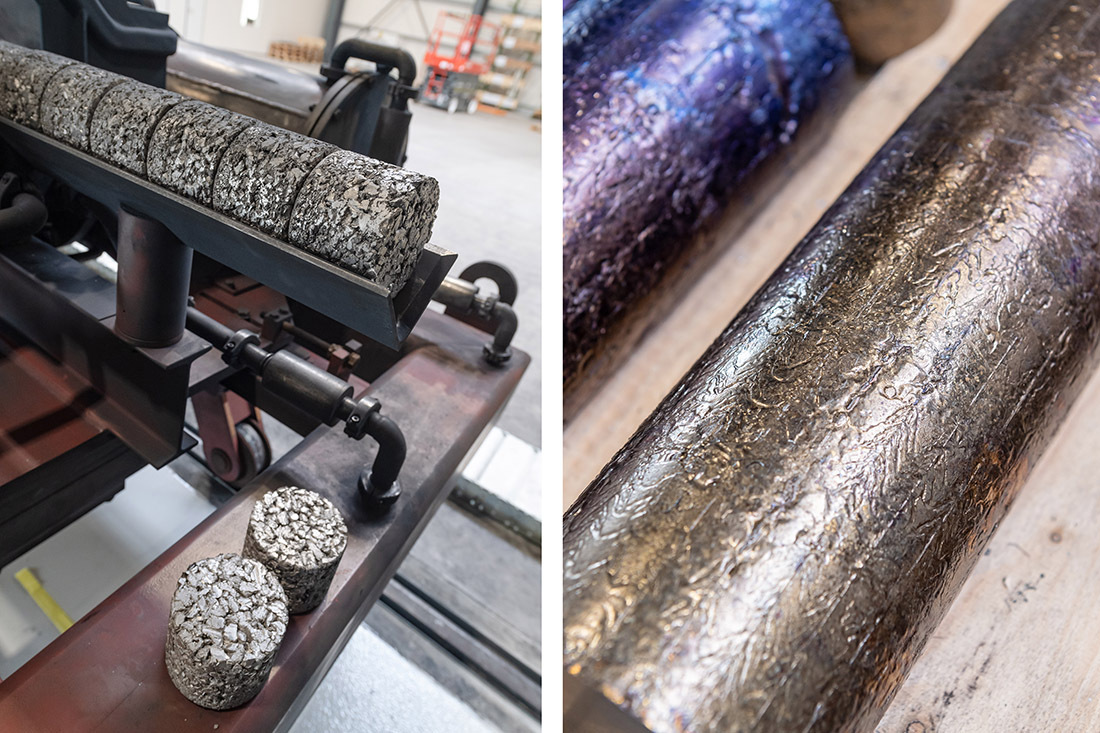
Mitigating development risks through loans and financial support
The Bremen-based company has worked closely together with funding institutions with the aim of mitigating the risks associated with development before they become an issue. HWH received financial assistance for technological developments from the LuFo V3 aviation research programme run by the German Federal Ministry for Economic Affairs and Climate Action. The BAB – the regional development bank for the state of Bremen and Bremerhaven – supplemented this funding with an FEI (Research, Development and Innovation) support package, which helped the company with its development efforts. Yet another financial boost came from a loan granted as part of the Bremen state investment support programme, which helped the company invest in production halls and machines. Last but not least came a commercial stake in the new area of business activity from the BAB venture capital fund, which boosted the company's equity capital.
Ina Meier-Buick, Manager of the Economic Development department at the BAB, regards HWH as an excellent role model: "A tailor-made combination of different funding programmes can really support a company in just the right place at just the right time. We're delighted that our programmes have contributed to the development of new expertise here in Bremen. This will enhance the city's long-term competitive position."
In addition to being a new area of expertise in Bremen, the smelter has already created four new jobs at HWH. "The support we received from the BAB over so many years was absolutely invaluable to us. The development bank stood shoulder-to-shoulder with us, every step of the way. Its consultants provided excellent advice and quickly became familiar with the commercial challenges we faced, and that was extremely helpful for us. We always felt that we were appreciated", remarked Hempel happily, describing the many successful years of working together.
Success Stories
Medium-Sized Companies in Bremen Showcasing the Full Range of the Local Economy
Medium-sized companies form the backbone of Bremen’s economy. They create jobs and produce goods that are in demand worldwide. Here is a selection of ten businesses that illustrate the diversity of Bremen’s economic landscape.
Learn moreTwelve international food and beverage companies in Bremen
Becks and Melitta may be high-profile brands, but international food and beverage companies also manufacture lots of other products in Bremen and Bremerhaven. Here are twelve examples.
Learn moreHow a space enthusiast campaigns for women in STEM fiels and Bremen as a space location
How does someone from a small village in Poland end up working on human spaceflight in Bremen? Dr. Anna Chrobry shares her journey through science, passion, and perseverance—and explains why she proudly calls herself a "space girl."
Learn more