Innovative Logistics at the Bremen Hansalinie Industrial Estate
Investing in BremenHow logistics companies' close proximity to the Mercedes Benz plant in Bremen is driving processes forward
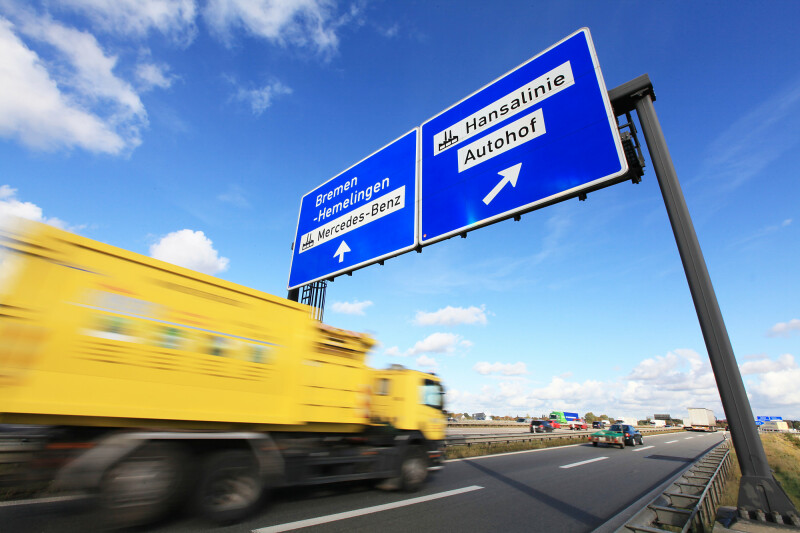
The Bremen Hansalinie Industrial Estate is a successful business park that is currently undergoing expansion. Several major logistics companies have based themselves here, developing increasingly sophisticated processes that aim to optimise just-in-sequence production for the automotive industry.
The success story of the Bremen Hansalinie Industrial Estate
The Bremen Hansalinie Industrial Estate has been a success story ever since it was established, experiencing a steady rate of development over the years. Its close proximity to the Mercedes-Benz plant in Bremen and its direct connection to the autobahn have resulted in continuous demand for the site. As a result, the industrial estate is currently undergoing its second stage of development, expanding by around 55 hectares. In recent years, Bremen has become a centre of excellence for the automotive industry, and the particular way in which it combines production, logistics, research and development has made it an especially attractive location for businesses. More than 20,000 people are employed in approximately 1,700 companies within the logistics industry here, covering the entire value chain. "The automotive and logistics industries are sectors that make Bremen a prime location for business," claims Ekkehart Siering, Permanent Secretary to Bremen's Senator for Economic Affairs, Labour and Ports.
The ever-expanding logistics companies supporting the automotive industry
"The Mercedes-Benz group is one of the main forces driving demand for the Bremen Hansalinie Industrial Estate," explains Jutta Zernikow, a project manager at Bremeninvest. Companies that have already been based at the business park for some time are continually looking to expand, and the site is welcoming new arrivals as well. For example, the Heddesheim-based pfenning logistics group opened a logistics centre at the industrial estate towards the end of 2015. The new building serves as the control centre for the just in-time supply of bodywork parts to the nearby Mercedes-Benz plant. It covers an area of 15,000 square metres and has provided 230 jobs for pfenning logistics employees.
The pfenning logistics transport cycle
Managing a three-shift operation and up to 1,000 journeys a day, pfenning logistics maintains a coordinated transport cycle that incorporates all the loading and unloading points of the Mercedes-Benz plant and supplier firms in the area as part of a just-in-time delivery system, supplying parts as and when they are required. Heavy goods vehicles deliver to the body shop units and all the other production halls at the Mercedes-Benz factory premises in Sebaldsbrück, Bremen. The company also provides services for other logistics firms in the local area.

Lorel's Plant Consolidation Center
The logistics provider Lorel has been based at the Bremen Hansalinie Industrial Estate for many years now. It operates a Plant Consolidation Center (PCC) at its site, using a sophisticated system to ensure that parts are supplied for just-in-time production. Lorel's 103,000 square metre premises incorporates a goods hall (65,000 square metres), a hall for empty container storage (16,500 square metres) and 10,000 square metres of outdoor storage. The PCC is a supplier-logistics centre that provides warehousing facilities for the automotive industry, from traditional goods storage to the handling of pre-picked goods, empty containers, and cross-docking. Lorel's PCC also provides the means for set assembly and package separation.
An IT system that supports separation of goods
Lorel's 400 employees dispatch a large number of heavy goods vehicles every day. To achieve this, every haulier making a delivery is allocated a certain time slot. By adhering to this time frame, the company can ensure that the deliveries are promptly processed. Side loading and unloading is standard practice at Lorel, also reducing the amount of time spent waiting at the gate. Lorel's IT System supports the separation of goods in the receiving area – through the use of cross-docking, items are directly transferred to the shipping area and subsequently transported to the plant.
Over 8,500 containers arrive at Lorel each day. 2,000 leave the warehouse again as soon as the cross-docking process is complete, while the rest remain in storage. Every storage rack is equipped with a radio frequency identification (RFID) tag. The driver of the reach truck picks up the goods indicated on the terminal and sees on the display which storage rack to place them in. Once they have been put away, the space they have been stored in is confirmed via the RFID reading and recorded in the system. This ensures that all storage operations are administered properly and booked in correctly, even when items are being lifted onto high shelf racks.
The goods retrieval process is controlled through a series of alerts that are determined by the production schedule. The retrieval alert messages include a product number, shift number and processing time. From the moment the alert is received, Lorel has 90 minutes to ready the goods for transport.
DB Schenker's logistics centre
DB Schenker also operates a supplier warehouse at the Bremen Hansalinie Industrial Estate that serves as an industrial park for the Mercedes-Benz plant nearby. More than 100 lorry loads a day are processed by around 320 DB Schenker employees in the receiving area before being placed in storage. The deliveries come from Germany and Europe, consisting of steering wheels, axles, suspension struts and other components. The employees put the required modules together in a way that facilitates the in-plant assembly process and deliver them in sequence to the Mercedes-Benz plant around six kilometres away. Schenker supplies parts for thousands of vehicles every week that are delivered in sync with the production process, arriving on the assembly lines exactly as and when they are needed.
The DB Schenker logistics centre at the industrial estate has continually grown in line with its customers' requirements. The project started in 2007 with around 10,000 square metres for storage and transshipment – today, DB Schenker manages an area nearly six times that size.
Good connections to Bremen's ports
The vehicles manufactured by the plant frequently pass through one of Bremen's ports on their outbound journey. The Bremen Hansalinie Industrial Estate provides easy access to these, possessing a good infrastructure of its own to boot. Besides offering excellent connections to the autobahn, the airport, the city centre, and its ports, the business park has a service area that is equipped with a petrol station, a wash for heavy goods vehicles, catering services and a hotel. "At the Bremen Hansalinie Industrial Estate, we have an ideal mix of sectors defined by the automotive industry, which will ensure the long-term success of the site," emphasises Jutta Zernikow.
For further information on the automotive and logistics sectors, please contact
Jutta Zernikow, tel: +49 (0)421 9600 249, jutta.zernikow@wfb-bremen.de,
Jörg Kautzner, tel: +49 (0)421 361-32172, joerg.kautzner@wah.bremen.de
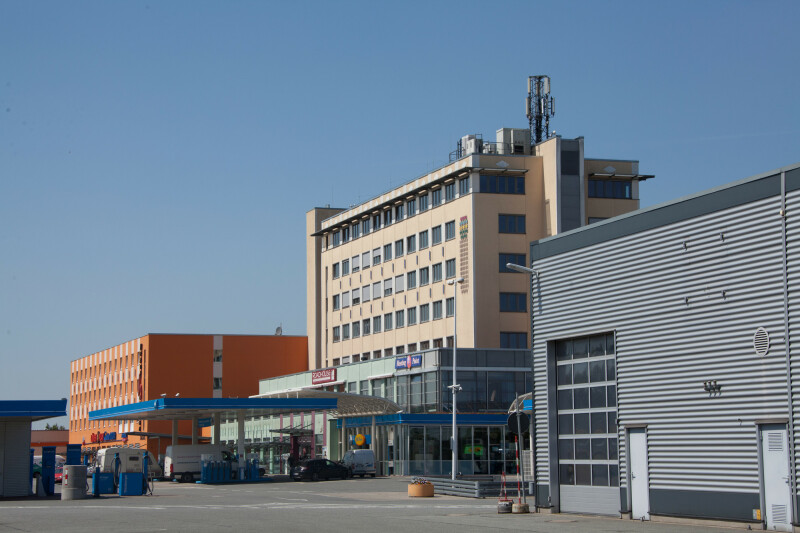
Success Stories
Medium-Sized Companies in Bremen Showcasing the Full Range of the Local Economy
Medium-sized companies form the backbone of Bremen’s economy. They create jobs and produce goods that are in demand worldwide. Here is a selection of ten businesses that illustrate the diversity of Bremen’s economic landscape.
Learn moreTwelve international food and beverage companies in Bremen
Becks and Melitta may be high-profile brands, but international food and beverage companies also manufacture lots of other products in Bremen and Bremerhaven. Here are twelve examples.
Learn moreTake-off for Bremen: what makes the city a hub for aerospace expertise
The sky is not the limit. Science, production, development and business all agree on this. Aircraft wings, Ariane rockets, Galileo satellites - Bremen is one of the top locations in the international aerospace industry. Five reasons for Bremen's success story.
Learn more